Steel-concrete composite tunnel lining supporting structure and manufacturing and construction method thereof
A supporting structure and concrete technology, applied in tunnel lining, tunnel, wellbore lining, etc., can solve the problems that the supporting strength cannot be strictly guaranteed, affect the progress of the project, and require large equipment investment, so as to save the back grouting process. , The effect of saving engineering volume and reducing equipment investment
- Summary
- Abstract
- Description
- Claims
- Application Information
AI Technical Summary
Problems solved by technology
Method used
Image
Examples
Embodiment Construction
[0066] The technical solution of the present invention will be further described below in conjunction with the accompanying drawings.
[0067] The first tunnel lining support structure of the present invention is formed by assembling curved unit plates 1 along the circumferential and axial directions of the tunnel wall; when assembled in the circumferential direction, adjacent unit plates 1 pass through side flanges 9 Connection, adjacent unit plates 1 are connected through end face flanges 8 during axial assembly. Since the unit plate 1 has a certain curvature, it has a pair of arc-shaped sides 2 and a pair of straight sides 3, and along the direction of the straight sides 3, ribs 4 are arranged at intervals on the inner wall of the unit plate 1 (that is, inside the arc), The number of ribs 4 is determined according to the actual situation. The radian of the ribs 4 is consistent with that of the arc-shaped side 2, or close to the arc-shaped side. A cavity cylinder 5 is formed...
PUM
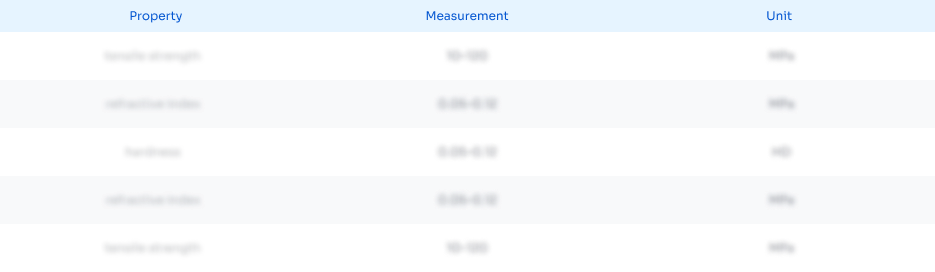
Abstract
Description
Claims
Application Information

- R&D
- Intellectual Property
- Life Sciences
- Materials
- Tech Scout
- Unparalleled Data Quality
- Higher Quality Content
- 60% Fewer Hallucinations
Browse by: Latest US Patents, China's latest patents, Technical Efficacy Thesaurus, Application Domain, Technology Topic, Popular Technical Reports.
© 2025 PatSnap. All rights reserved.Legal|Privacy policy|Modern Slavery Act Transparency Statement|Sitemap|About US| Contact US: help@patsnap.com