LED heat-dissipation fiber coating and preparation method therefor
A fiber and coating technology, applied in the field of LED heat dissipation fiber coating and its preparation, can solve the problem of difficult dispersion of carbon nanotubes, and achieve the effect of improving the dispersion effect and improving the impact strength.
- Summary
- Abstract
- Description
- Claims
- Application Information
AI Technical Summary
Problems solved by technology
Method used
Examples
Embodiment Construction
[0027] A kind of led heat dissipation fiber coating, it is made up of the following raw materials of weight part:
[0028] High-density polyethylene 360, sodium hydroxide 100, bisphenol A400, epichlorohydrin 160, silicon nitride 10, acrylamide 2, ammonium chloride 1, N, N methylenebisacrylamide 0.05, ammonium persulfate 3 , TritonX1140.01, ammonia water 1.8, diethylenetriamine 10, carbon nanotubes 30, precipitated barium sulfate 20, ammonium metaborate 2, ethyl cellulose 3, dimethyl methylphosphonate 5, calcined kaolin 18, Polyoxypropylene glycol 5, lauroyl diethanolamine 0.7.
[0029] A kind of preparation method of described led heat dissipation fiber coating, comprises the following steps:
[0030] (1) Add water to the above sodium hydroxide to prepare a 10% sodium hydroxide solution;
[0031] (2) Mix carbon nanotubes, silicon nitride, and ammonium chloride, and ball mill them evenly;
[0032] (3) Add the above-mentioned lauroyl diethanolamine to 16 times of water, add e...
PUM
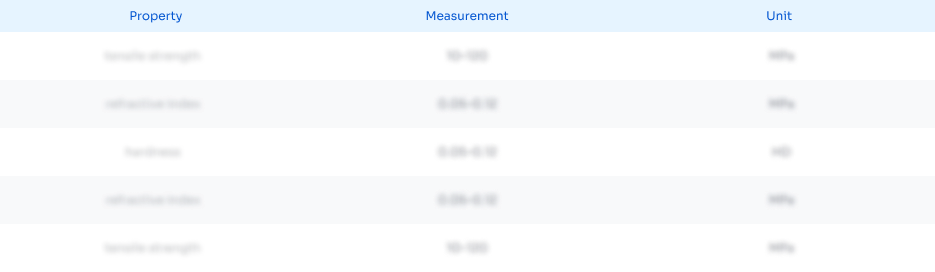
Abstract
Description
Claims
Application Information

- R&D Engineer
- R&D Manager
- IP Professional
- Industry Leading Data Capabilities
- Powerful AI technology
- Patent DNA Extraction
Browse by: Latest US Patents, China's latest patents, Technical Efficacy Thesaurus, Application Domain, Technology Topic, Popular Technical Reports.
© 2024 PatSnap. All rights reserved.Legal|Privacy policy|Modern Slavery Act Transparency Statement|Sitemap|About US| Contact US: help@patsnap.com