Method for producing potassium sulfate from potassium/chlorine-ion-containing solid waste
A technology of potassium sulfate and chloride ions, applied in chemical instruments and methods, alkali metal sulfite/sulfite, alkali metal compounds, etc., can solve problems such as large equipment investment, high processing cost, hidden safety hazards in production management, etc. Achieve cost saving, cost reduction and high product quality
- Summary
- Abstract
- Description
- Claims
- Application Information
AI Technical Summary
Problems solved by technology
Method used
Image
Examples
Embodiment 1
[0032] 1. Remove impurities
[0033] To the leaching wastewater containing potassium and chloride ion solid waste (main component: K 2 O content is 5.1%, Cl ion content is 5.9%), add saturated lime water to adjust the pH value=7.5 of solution, after stirring and removing impurity 60min, add ammonium bicarbonate (addition is 0.09% of solution weight) in solution , after stirring for 60 minutes to remove impurities, filter, and the filtrate enters the buffer tank for later use.
[0034] 2. Concentration
[0035] Add the impurity removal solution in the buffer tank to the three-effect falling film evaporator and concentrate to K + The content is 128g / L, and the concentrate enters the buffer tank.
[0036] 2. Potassium sulfate formation reaction
[0037]The concentrate in the buffer tank is added to the reaction tank, and simultaneously add the ammonium sulfate solid (the mass ratio of ammonium sulfate and potassium ion=2.7) of solution weight 34.8% and the potassium sulfate c...
Embodiment 2
[0057] 1. Remove impurities
[0058] To the leaching wastewater containing potassium and chloride ion solid waste (main component: main component: K 2 O content is 5.1%, Cl ion content is 5.9%), add saturated lime water to adjust the pH value=9.0 of solution, after stirring and removing impurity 60min, add ammonium bicarbonate (addition is 0.12% of solution weight) in solution , after stirring for 60 minutes to remove impurities, filter, and the filtrate enters the buffer tank for later use.
[0059] 2. Concentration
[0060] Add the impurity removal solution in the buffer tank to the three-effect falling film evaporator and concentrate to K + The content is 128g / L, and the concentrate enters the buffer tank.
[0061] 2. Potassium sulfate formation reaction
[0062] The concentrate in the buffer tank is added to the reaction tank, and the ammonium sulfate solid (the mass ratio of ammonium sulfate and potassium ion=2.7) and 1.21% of the potassium sulfate crystal growth acce...
Embodiment 3
[0076] 1. Remove impurities
[0077] To the leaching wastewater containing potassium and chloride ion solid waste (main component: main component: K 2 O content is 5.1%, Cl ion content is 5.9%), add saturated lime water to adjust the pH value=10.0 of solution, after stirring and removing impurity 60min, add ammonium bicarbonate (addition is 0.15% of solution weight) in solution , after stirring for 60 minutes to remove impurities, filter, and the filtrate enters the buffer tank for later use.
[0078] 2. Concentration
[0079] Add the impurity removal solution in the buffer tank to the three-effect falling film evaporator and concentrate to K + The content is 128g / L, and the concentrate enters the buffer tank.
[0080] 2. Potassium sulfate formation reaction
[0081] The concentrated solution in the buffer tank is added to the reaction tank, and the ammonium sulfate solid (the mass ratio of ammonium sulfate and potassium ion=3.05) and 1.0% of the potassium sulfate crystal ...
PUM
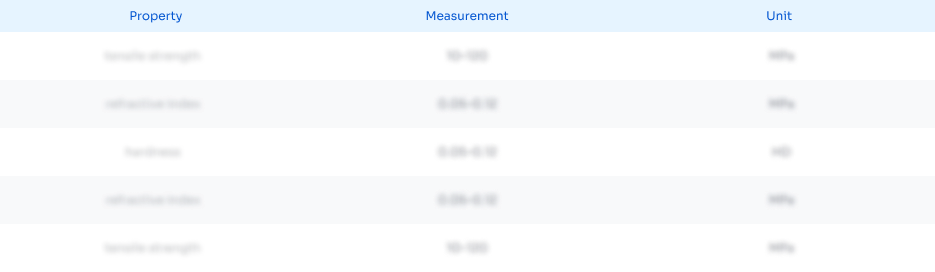
Abstract
Description
Claims
Application Information

- Generate Ideas
- Intellectual Property
- Life Sciences
- Materials
- Tech Scout
- Unparalleled Data Quality
- Higher Quality Content
- 60% Fewer Hallucinations
Browse by: Latest US Patents, China's latest patents, Technical Efficacy Thesaurus, Application Domain, Technology Topic, Popular Technical Reports.
© 2025 PatSnap. All rights reserved.Legal|Privacy policy|Modern Slavery Act Transparency Statement|Sitemap|About US| Contact US: help@patsnap.com