Multistage coaxial alternating type extrusion device
A staggered, coaxial technology, applied in the fields of mixing and extrusion molding equipment, crushing, and material grinding, it can solve the problem of limited extrusion, crushing and grinding force, not suitable for strong crushing and grinding, manufacturing and use costs Advanced problems, to achieve the effect of improving efficiency and grinding quality, compact structure, and simplified machine structure
- Summary
- Abstract
- Description
- Claims
- Application Information
AI Technical Summary
Problems solved by technology
Method used
Image
Examples
Embodiment Construction
[0029] The specific embodiments of the present invention will be further described below in conjunction with the accompanying drawings. It should be noted here that the descriptions of these embodiments are used to help understand the present invention, but are not intended to limit the present invention. In addition, the technical features involved in the various embodiments of the present invention described below may be combined with each other as long as they do not constitute a conflict with each other.
[0030] In the description of the present invention, the orientations or positional relationships indicated by the terms "left", "right", etc. are based on the orientations or positional relationships shown in the drawings. construction and operation, therefore, should not be construed as limiting the invention.
[0031] In the description of the present invention, the terms "first" and "second" are used for descriptive purposes only, and should not be understood as indi...
PUM
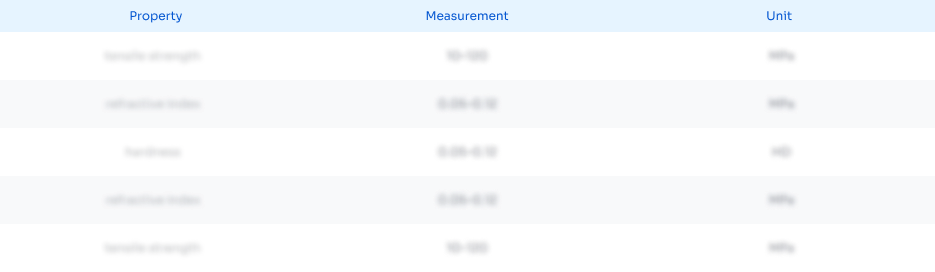
Abstract
Description
Claims
Application Information

- R&D Engineer
- R&D Manager
- IP Professional
- Industry Leading Data Capabilities
- Powerful AI technology
- Patent DNA Extraction
Browse by: Latest US Patents, China's latest patents, Technical Efficacy Thesaurus, Application Domain, Technology Topic, Popular Technical Reports.
© 2024 PatSnap. All rights reserved.Legal|Privacy policy|Modern Slavery Act Transparency Statement|Sitemap|About US| Contact US: help@patsnap.com