Energy-saving hydrogen decrepitation device for production of rare earth magnetic materials
A magnetic material and rare earth technology, which is applied in the field of energy-saving hydrogen crushing devices for the production of rare earth magnetic materials, can solve the problems of low milling efficiency, waste of heat, and high energy costs of enterprises, so as to save warm-up time and reduce energy consumption. Cost, the effect of improving milling efficiency
- Summary
- Abstract
- Description
- Claims
- Application Information
AI Technical Summary
Problems solved by technology
Method used
Image
Examples
Embodiment Construction
[0018] In order to make the technical means, creative features, goals and effects achieved by the present invention easy to understand, the present invention will be further described below in conjunction with specific illustrations.
[0019] see Figure 1 ~ Figure 3 An energy-saving hydrogen crushing device for the production of rare earth magnetic materials, including a front heating chamber 1, a rotating heating chamber 2, a rear heating chamber 3, a guide rail 4, a reaction furnace 5, a reaction furnace installation frame 6, a fixed pin 7, a sliding frame 8, Connecting rod 9, slide front stop pin 10, slide back stop pin 11, pulley 12, heating pipe 13, heat insulation layer 14, baffle plate 15, travel switch 16 and limit frame 17.
[0020] In this embodiment, the front group hydrogen crushing mechanism, the middle group hydrogen crushing mechanism and the rear group hydrogen crushing mechanism are installed on the guide rail 4, wherein the front group hydrogen crushing mech...
PUM
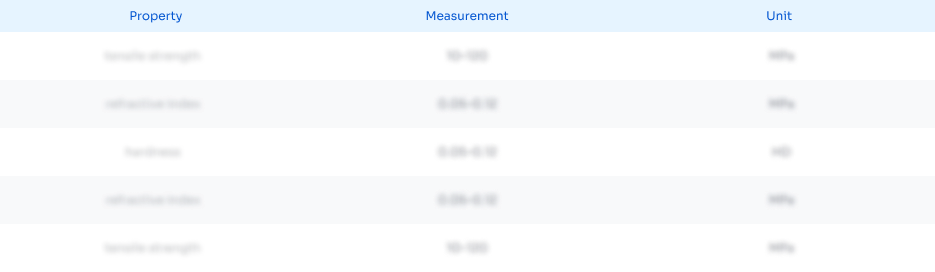
Abstract
Description
Claims
Application Information

- R&D
- Intellectual Property
- Life Sciences
- Materials
- Tech Scout
- Unparalleled Data Quality
- Higher Quality Content
- 60% Fewer Hallucinations
Browse by: Latest US Patents, China's latest patents, Technical Efficacy Thesaurus, Application Domain, Technology Topic, Popular Technical Reports.
© 2025 PatSnap. All rights reserved.Legal|Privacy policy|Modern Slavery Act Transparency Statement|Sitemap|About US| Contact US: help@patsnap.com