Air-ground dual-purpose composite heat insulation structure based on air cooling screen
An adiabatic structure and air-cooling technology, which is applied to heat exchange equipment, protects pipes through heat insulation, heat preservation, etc., can solve the problem of heat leakage, the problem of meeting the overall quality requirements of spacecraft, and the inability of multi-layer insulation layers to insulate heat, etc. problem, to achieve the effect of light weight, low density and reduced mass
- Summary
- Abstract
- Description
- Claims
- Application Information
AI Technical Summary
Problems solved by technology
Method used
Image
Examples
Embodiment Construction
[0019] Such as figure 1 As shown, the ground-air dual-purpose thermal insulation structure based on the air-cooled screen of the present invention includes: a polyurethane foam insulation layer 3, a variable-density insulation layer 4, and an air-cooled screen 5;
[0020] Paste a layer of polyurethane foam heat insulation layer 3 on the outside of the low-temperature storage tank 2, and coat a layer of variable density heat insulation layer 4 on the outside of the polyurethane foam heat insulation layer 3;
[0021] The thermal conductivity of the polyurethane foam insulation layer 3 is low, and it mainly plays an insulating role during the parking and launch stages of the spacecraft. The density of the polyurethane foam in the polyurethane foam insulation layer is about 30-46kg / m in the temperature range of 77-300K 3 , The thermal conductivity is about 0.018-0.026W / (m·K).
[0022] Each layer of the variable density heat insulation layer 4 includes a radiation layer material a...
PUM
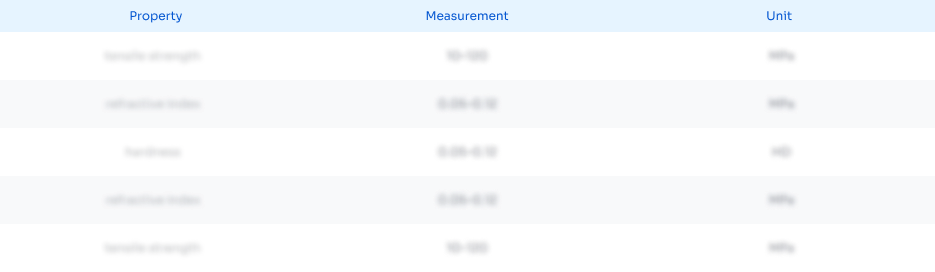
Abstract
Description
Claims
Application Information

- Generate Ideas
- Intellectual Property
- Life Sciences
- Materials
- Tech Scout
- Unparalleled Data Quality
- Higher Quality Content
- 60% Fewer Hallucinations
Browse by: Latest US Patents, China's latest patents, Technical Efficacy Thesaurus, Application Domain, Technology Topic, Popular Technical Reports.
© 2025 PatSnap. All rights reserved.Legal|Privacy policy|Modern Slavery Act Transparency Statement|Sitemap|About US| Contact US: help@patsnap.com