Low-alloy gray cast iron material for truck brake drums and preparation method thereof
A brake drum and low-alloy technology, applied in casting molding equipment, metal processing equipment, casting molds, etc., can solve problems such as safety accidents, performance limitations, frequent replacement, etc., to avoid shrinkage and shrinkage cavities, improve strength, and cast The effect of simple process operation
- Summary
- Abstract
- Description
- Claims
- Application Information
AI Technical Summary
Problems solved by technology
Method used
Image
Examples
preparation example Construction
[0028] A kind of preparation method of low-alloy gray cast iron material for truck brake drum of the present invention, the method comprises the following steps:
[0029] (1) Molten iron smelting: prepare raw materials according to the formula quantity, add the prepared raw materials to an intermediate frequency induction furnace for heating and smelting to obtain alloy molten iron; when the temperature of alloy molten iron reaches 1480-1550°C, it is released from the furnace;
[0030] (2) Inoculation treatment: place the inoculant in the ladle, pour into the alloy molten iron, and perform gray iron inoculation treatment. The inoculation time is 30s to 120s. Stir to remove slag. After the gray iron molten iron is processed, prepare for subsequent pouring; The inoculant is preferably a silicon barium inoculant, and the added amount is 0.8-1.2% of the total mass of raw materials.
[0031] (3) Pouring process: pour the molten gray iron inoculated in step (2) into the cavity of th...
Embodiment 1
[0033] The formula composition and mass percentage are: C: 3.25%, Si: 1.59%, Mn: 0.42%, S: 0.029%, P: 0.043%, Mg: 0.035%, Cr: 0.4%, V: 0.27%, Ni: 0.31 %, Cu: 0.5%, Mo: 0.30%, Sn: 0.06%, and the balance is iron.
[0034] Preparation method: (1) Molten iron smelting: prepare raw materials according to the formula quantity, add the prepared raw materials to an intermediate frequency induction furnace for heating and smelting to obtain alloy molten iron; wait until the temperature of the molten iron reaches: 1520°C to be released from the furnace;
[0035] (2) Inoculation treatment: the inoculant is placed in the ladle, poured into the alloy molten iron, and the gray iron inoculation treatment is carried out. The inoculation time is 50s, and the slag is removed by stirring. After the molten iron is processed, the subsequent pouring is prepared; the silicon barium inoculant ( JFB2) add-on is 0.9% of raw material.
[0036] (3) Casting process: pour the gray iron molten iron inocula...
Embodiment 2
[0038] The formula composition and mass percentage are: C: 3.10%, Si: 1.55%, Mn: 0.40%, S: 0.025%, P: 0.044%, Mg: 0.03%, Cr: 0.25%, V: 0.25%, Ni: 0.25 %, Cu: 0.35%, Mo: 0.25%, Sn: 0.05%, and the balance is iron.
[0039] Preparation method: (1) Molten iron smelting: Prepare raw materials according to the formula quantity, add the prepared raw materials to an intermediate frequency induction furnace for heating and melting to obtain alloy molten iron; wait until the temperature of the molten iron reaches: 1490°C to be released from the furnace;
[0040] (2) Inoculation treatment: the inoculant is placed in the ladle, poured into the alloy molten iron, and the gray iron inoculation treatment is carried out. The inoculation time is 50s, and the slag is removed by stirring. After the molten iron is processed, the subsequent pouring is prepared; the silicon barium inoculant ( JFB2) add-on is 0.9% of raw material.
[0041] (3) Casting process: pour the gray iron molten iron inocula...
PUM
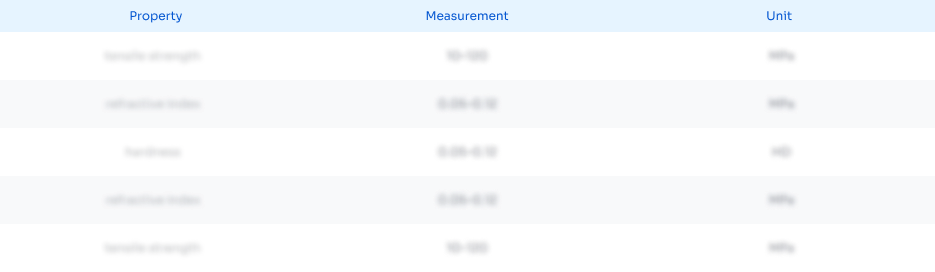
Abstract
Description
Claims
Application Information

- R&D
- Intellectual Property
- Life Sciences
- Materials
- Tech Scout
- Unparalleled Data Quality
- Higher Quality Content
- 60% Fewer Hallucinations
Browse by: Latest US Patents, China's latest patents, Technical Efficacy Thesaurus, Application Domain, Technology Topic, Popular Technical Reports.
© 2025 PatSnap. All rights reserved.Legal|Privacy policy|Modern Slavery Act Transparency Statement|Sitemap|About US| Contact US: help@patsnap.com