Preparation method of foamed polyester slurry
A polyester pulp and foaming technology, which is applied in the field of water-soluble polyester pulp preparation, can solve the problems of different purposes, consume a lot of steam, and take a long time for pulping, so as to increase the specific surface area and speed up the dissolution rate. Effect
- Summary
- Abstract
- Description
- Claims
- Application Information
AI Technical Summary
Problems solved by technology
Method used
Image
Examples
Embodiment 1
[0022] The preparation method includes the following process steps:
[0023] (1) 750kg of waste recycled polyester plastic (with moisture content within 6%),
[0024] Ethylene glycol 280kg (over 200% excess),
[0025] Isophthalic acid 50kg,
[0026] 100kg of isophthalic acid-5-sodium sulfonate,
[0027] Sb 2 O 3 120g,
[0028] The above components are mixed and put into a 1.8 cubic cone-bottom jacketed kettle type polymerization kettle, and the temperature rises at a static normal pressure. In this process, the top temperature of the fractionation column of the reactor is controlled at 105 ° C ± 3 ° C in the initial stage. When the temperature reaches 235°C±5°C, the material is completely melted, and when the distilled water and / or methanol reaches 90-100% of the theoretical distillate, the internal temperature is raised to 250-260°C, and the excess ethylene glycol is distilled out;
[0029] (2) After the above pre-melting reaction is completed, the material is introduce...
Embodiment 2
[0035] The preparation method includes the following process steps:
[0036] (1) 750kg of waste recycled polyester plastic (with moisture content within 6%),
[0037] Ethylene glycol 300kg (over 240% excess),
[0038] Isophthalic acid 75kg,
[0039] 75kg of isophthalic acid-5-sodium sulfonate,
[0040] Sb 2 O 3 120g,
[0041] The above components are mixed and put into a 1.8 cubic cone-bottom jacketed kettle type polymerization kettle, and the temperature rises at a static normal pressure. In this process, the top temperature of the fractionation column of the reactor is controlled at 105 ° C ± 3 ° C in the initial stage. When the temperature reaches 235°C±5°C, the material is completely melted, and when the distilled water and / or methanol reaches 90-100% of the theoretical distillate, the internal temperature is raised to 250-260°C, and the excess ethylene glycol is distilled out;
[0042] (2) After the above pre-melting reaction is completed, the material is introduced...
Embodiment 3
[0048] The preparation method comprises the following process steps:
[0049] (1) 800kg of waste recycled polyester plastic (moisture content within 6%),
[0050] Ethylene glycol 300kg (more than 180% in excess),
[0051] Isophthalic acid 50kg,
[0052] Sodium isophthalic acid-5-sulfonate 125kg,
[0053] Sb 2 o 3 120g,
[0054] Mix the above components and put them together into a 1.8 cubic cone-bottomed jacketed kettle-type polymerization kettle, and raise the temperature under static normal pressure. During this process, the top temperature of the reaction kettle fractionation column is controlled at 105°C ± 3°C at the beginning stage. When the reaction internal temperature When the temperature reaches 235°C±5°C, the material is completely melted, and when the distilled water and / or methanol reaches 90-100% of the theoretical distilled amount, then raise the internal temperature to 250-260°C to distill out excess ethylene glycol;
[0055] (2) After the above pre-meltin...
PUM
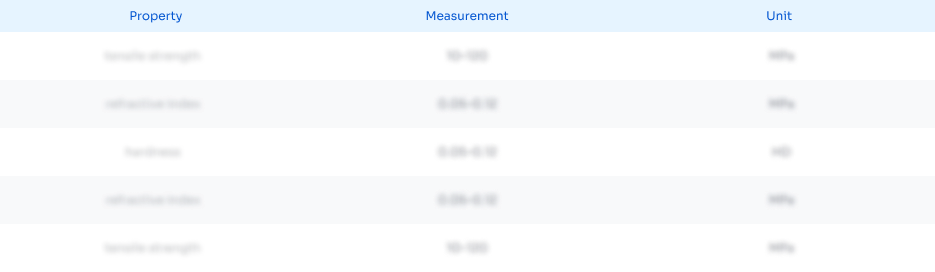
Abstract
Description
Claims
Application Information

- Generate Ideas
- Intellectual Property
- Life Sciences
- Materials
- Tech Scout
- Unparalleled Data Quality
- Higher Quality Content
- 60% Fewer Hallucinations
Browse by: Latest US Patents, China's latest patents, Technical Efficacy Thesaurus, Application Domain, Technology Topic, Popular Technical Reports.
© 2025 PatSnap. All rights reserved.Legal|Privacy policy|Modern Slavery Act Transparency Statement|Sitemap|About US| Contact US: help@patsnap.com