Blanking mold
A blanking die and punching technology, which is applied in the direction of manufacturing tools, metal processing equipment, stripping devices, etc., can solve the problems of low edge strength and cannot be re-sharpened, achieve smooth punching edges without burrs, and increase the number of molds The effect of repeated sharpening and repair times and high workpiece quality
- Summary
- Abstract
- Description
- Claims
- Application Information
AI Technical Summary
Problems solved by technology
Method used
Image
Examples
Embodiment Construction
[0011] The present invention will be described in further detail below by means of specific embodiments:
[0012] The reference numerals in the accompanying drawings of the specification include: the lower mold base 1, the upper mold base 2, the punch 4, the second spring 5, the first spring 6, the die 7, the beam 8, the connecting rod 9, and the guide channel 10.
[0013] The embodiment is basically as attached figure 1 Shown: a blanking die, including a mold base, a punch 4 and a die 7, the mold base includes an upper mold base 2 and a lower mold base 1, the die 7 is connected to the upper mold base 2, and the punch 4 is connected to the lower mold base 1. The lower mold base 1 is connected; the upper mold base 2 is also connected to the beam 8, the beam 8 is provided with a first spring 6, one end of the connecting rod 9 is disc-shaped and is located in the die 7, and the connecting rod 9 is connected to the first spring 6; A second spring 5 is installed on the punch 4; th...
PUM
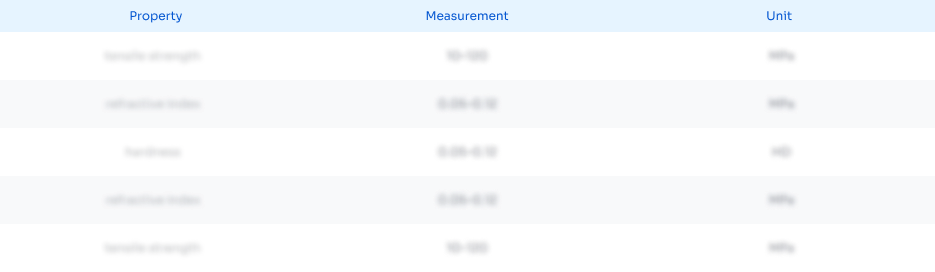
Abstract
Description
Claims
Application Information

- Generate Ideas
- Intellectual Property
- Life Sciences
- Materials
- Tech Scout
- Unparalleled Data Quality
- Higher Quality Content
- 60% Fewer Hallucinations
Browse by: Latest US Patents, China's latest patents, Technical Efficacy Thesaurus, Application Domain, Technology Topic, Popular Technical Reports.
© 2025 PatSnap. All rights reserved.Legal|Privacy policy|Modern Slavery Act Transparency Statement|Sitemap|About US| Contact US: help@patsnap.com