Method of preparing ganged brick by using aluminum scruff ash
A technology of waste aluminum ash and clear water bricks, which is applied to clay products, other household appliances, household appliances, etc. It can solve the problems of unfinished engineering research, in its infancy, and low yield of finished products, so as to prevent cracks and delamination , Inhibition of deformation, strong frost resistance
- Summary
- Abstract
- Description
- Claims
- Application Information
AI Technical Summary
Problems solved by technology
Method used
Examples
Embodiment 1
[0020] A kind of method that waste aluminum ash prepares clear water brick, comprises the following steps:
[0021] (100) The raw material selection consists of the following components by mass percentage: 60% waste aluminum ash, 20% shale, 10% quartz and 10% additives; the additives are composed of the following components: limestone, magnesite and Spodumene, the mass ratio of limestone, magnesite and spodumene is 1:1:1;
[0022] (200) Mixing the above-mentioned raw materials according to the mass percentage evenly, and after vibration milling, use a ball mill to mill for 45-65 minutes, preferably 60 minutes, to obtain a powder;
[0023] (300) pulping the above powder, adding glue and granulating, and then pressing and molding the powder by semi-dry pressing to obtain a molded blank; the water content of the particles after adding glue and granulating is less than 10%, generally controlled at 4 %-7%;
[0024] (400) drying the above formed blank in a drying tower at a drying...
Embodiment 2
[0028] A kind of method that waste aluminum ash prepares clear water brick, comprises the following steps:
[0029] (100) The raw material selection consists of the following components by mass percentage: 63% waste aluminum ash, 16% shale, 8% quartz and 13% additives; the additives are composed of the following components: limestone, magnesite and Spodumene, the mass ratio of limestone, magnesite and spodumene is 1:1:1;
[0030] (200) Mixing the above-mentioned raw materials according to the mass percentage evenly, and after vibration milling, use a ball mill to mill for 45-65 minutes, preferably 60 minutes, to obtain a powder;
[0031] (300) pulping the above powder, adding glue and granulating, and then pressing and molding the powder by semi-dry pressing to obtain a molded blank; the water content of the particles after adding glue and granulating is less than 10%, generally controlled at 4 %-7%;
[0032] (400) drying the above formed blank in a drying tower at a drying ...
PUM
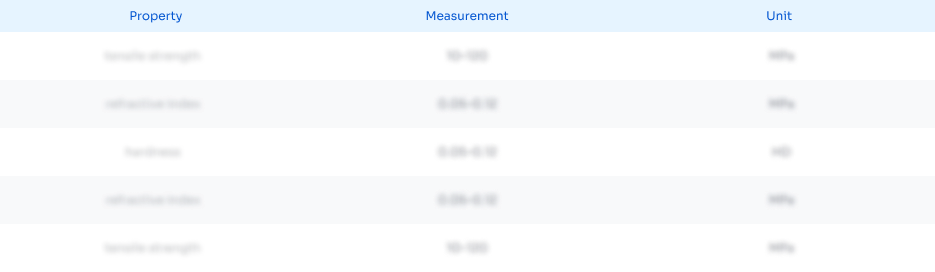
Abstract
Description
Claims
Application Information

- R&D Engineer
- R&D Manager
- IP Professional
- Industry Leading Data Capabilities
- Powerful AI technology
- Patent DNA Extraction
Browse by: Latest US Patents, China's latest patents, Technical Efficacy Thesaurus, Application Domain, Technology Topic, Popular Technical Reports.
© 2024 PatSnap. All rights reserved.Legal|Privacy policy|Modern Slavery Act Transparency Statement|Sitemap|About US| Contact US: help@patsnap.com