Silyl ether mixed defoaming agent emulsion and preparation method thereof
A technology of defoamer and composite emulsifier, applied in the direction of foam dispersion/prevention, etc., can solve problems such as poor water solubility, emulsion instability, easy demulsification, etc., achieve stable emulsion stability, benefit mass production, and chemical properties inert effect
- Summary
- Abstract
- Description
- Claims
- Application Information
AI Technical Summary
Problems solved by technology
Method used
Image
Examples
Embodiment 1
[0027] Mix 100 parts of linear dimethyl silicone oil with 3 parts of modified white carbon black evenly, heat up to 130°C; add 3 parts of triethanolamine, stir for 3 hours, then cool to 90°; add 40 parts of allyl ether modified silicone oil and 25 parts of polyoxypropylene glyceryl ether, after continuing to stir for one hour; add 10 parts of compound emulsifiers and stir at a high speed to form a coarse emulsion, wherein the compound emulsifiers are mixed by 5 parts of Tween-80 and 5 parts of soybean lecithin; then Add 320mL of 0.5% hydroxymethyl cellulose thickening water to the coarse emulsion to prepare an emulsion with a solid content of 35%; then pour the emulsion into a high-speed homogenizer and stir at 12000r / min for 20min. A fine and stable microemulsion is formed; this microemulsion can be centrifuged in a 5000r / min centrifuge for 5 minutes without stratification.
[0028] Test method: Pour 100mL of bubbling liquid into a 500mL measuring cylinder, insert the glass t...
Embodiment 2
[0033] Mix 100 parts of linear dimethyl silicone oil with 5 parts of modified silica evenly, heat up to 130°C; add 5 parts of triethanolamine, stir for 3 hours, then cool to 80°; add 50 parts of allyl ether to modify Silicone oil and 35 parts of polyoxypropylene glyceryl ethers, continue to stir for 1h; Add 7 parts of compound emulsifiers and stir at high speed to form a coarse emulsion, wherein the compound emulsifiers are mixed by 3.5 parts of Tween-80 and 3.5 parts of soybean lecithin; Add 360mL of 0.5% hydroxymethylcellulose thickening water to the coarse emulsion to prepare an emulsion with a solid content of 35%; then pour the emulsion into a high-speed homogenizer and stir at 12000r / min for 25min to form Delicate and stable microemulsion; this microemulsion can guarantee that it will not be separated when centrifuged in a 5000r / min centrifuge for 5 minutes.
[0034] Test method: 35kg fermentation broth base material, 50L fermentation tank, first add 5g polyether defoame...
Embodiment 3
[0039] Mix 100 parts of linear dimethyl silicone oil with 3 parts of modified silica evenly, heat up to 130°C; add 2 parts of triethanolamine, stir for 3 hours, then cool to 80°C; then add 30 parts of allyl ether modified silicone oil And 30 parts of polyoxypropylene glyceryl ethers, continue to stir for 1h; Add 8 parts of compound emulsifiers and stir at high speed to form a coarse emulsion, wherein the compound emulsifiers are mixed by 4 parts of Tween-80 and 4 parts of soybean lecithin; Add 480mL of hydroxymethyl cellulose thickening water with a mass concentration of 0.3% to the emulsion to prepare an emulsion with a solid content of 25%; then pour the emulsion into a high-speed homogenizer and stir at a high speed of 12000r / min for 20min to form Delicate and stable microemulsion; this microemulsion can guarantee that it will not be separated in a 3000r / min centrifuge for 5 minutes.
[0040] Test method: 35kg fermentation broth base material, 50L fermentation tank, first a...
PUM
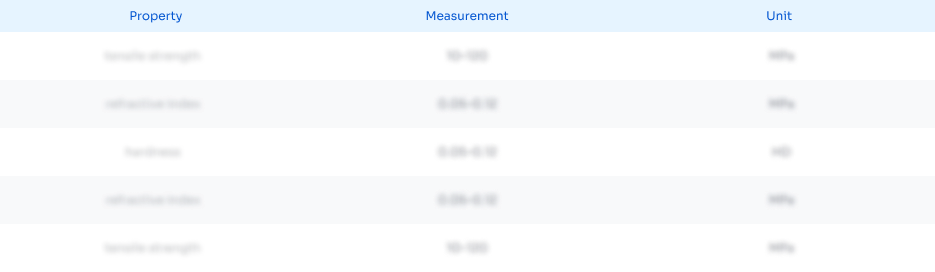
Abstract
Description
Claims
Application Information

- R&D
- Intellectual Property
- Life Sciences
- Materials
- Tech Scout
- Unparalleled Data Quality
- Higher Quality Content
- 60% Fewer Hallucinations
Browse by: Latest US Patents, China's latest patents, Technical Efficacy Thesaurus, Application Domain, Technology Topic, Popular Technical Reports.
© 2025 PatSnap. All rights reserved.Legal|Privacy policy|Modern Slavery Act Transparency Statement|Sitemap|About US| Contact US: help@patsnap.com