a gas combustion chamber
A combustion chamber and combustion chamber technology, which is applied in the direction of using a variety of fuel combustion, combustion types, combustion equipment, etc., can solve the problems of short gas residence time, high energy consumption, low combustion rate, etc., to save purification treatment costs, The overall structure is simple and the effect of increasing the contact time
- Summary
- Abstract
- Description
- Claims
- Application Information
AI Technical Summary
Problems solved by technology
Method used
Image
Examples
Embodiment 1
[0022] The present invention provides a gas combustion chamber, such as figure 2 As shown, it includes a casing 1 with a combustion chamber 11 inside. The casing 1 can be designed as a cuboid, cube or other shapes as a whole. Air inlet 13, wherein, the inner wall of gas inlet 13 is provided with a refractory layer 6, which improves the fire resistance and service life of the gas conduit. The left and right sides of the casing 1 are respectively provided with a first burner 2 and a second burner 3 communicating with the combustion chamber 11. The first burner 2 and the second burner 3 are arranged horizontally opposite each other. The first burner 2 It is arranged on the same side as the gas inlet 13 and is located below the gas inlet 13 . A heat insulating block 5 is arranged between the first burner 2 and the gas inlet 13 to prevent the high temperature generated by the second burner 3 from damaging the gas inlet pipe.
[0023] In order to prevent the two burners from burn...
Embodiment 2
[0027] Such as Figure 4 As shown, the components that are the same as or corresponding to those in the first embodiment are marked with the corresponding reference numerals in the first embodiment. For the sake of simplicity, only the differences from the first embodiment will be described below. This embodiment two and figure 2 The difference of the first shown embodiment is that the number of air barriers 4 in this embodiment is more than two, such as two, three or four, which are set according to the length of the combustion chamber 11 and the actual working requirements, and Adjacent gas-blocking walls 4 are arranged staggered up and down on the inner wall of housing 1, so that the high-temperature flue gas and incompletely burned gas generated by the combustion of the gas through the first burner 2 run along the surface of the gas-blocking wall 4 and the ends of the gas-blocking wall 4 The high-temperature flue gas channel 14 flows between the upper part and the inner ...
PUM
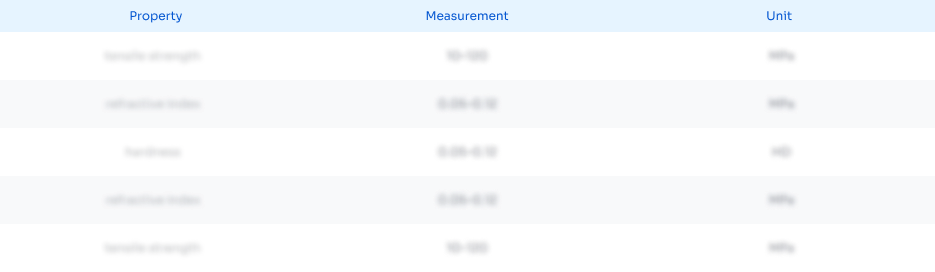
Abstract
Description
Claims
Application Information

- R&D
- Intellectual Property
- Life Sciences
- Materials
- Tech Scout
- Unparalleled Data Quality
- Higher Quality Content
- 60% Fewer Hallucinations
Browse by: Latest US Patents, China's latest patents, Technical Efficacy Thesaurus, Application Domain, Technology Topic, Popular Technical Reports.
© 2025 PatSnap. All rights reserved.Legal|Privacy policy|Modern Slavery Act Transparency Statement|Sitemap|About US| Contact US: help@patsnap.com