Bidirectional prefabricated segment splicing construction method for large-sized underpass
A large-size, large-segment technology, which is applied in the field of two-way prefabricated segmental assembly of large-scale underpasses, can solve problems such as increased construction difficulty, high labor intensity, and slow progress, and achieves construction quality assurance, reduced interference, and The effect of speeding up the construction progress
- Summary
- Abstract
- Description
- Claims
- Application Information
AI Technical Summary
Problems solved by technology
Method used
Image
Examples
Embodiment 1
[0044] Such as Figure 1-4 As shown, the closed prefabricated section is a single hole prefabricated section, which includes an inverted U-shaped prefabricated section 1, a U-shaped prefabricated section 2, a shear key 3, a shear keyway 4, a pre-embedded steel plate 5, a corrugated The pipe 6 and the steel plate waterstop 7, the lower end of the inverted U-shaped prefabricated section 1 is matched and spliced with the upper end of the U-shaped prefabricated section 2, and the shear force key 3 and the shear force keyway 4 are used to cooperate at the splicing surface. The pre-embedded steel plate 5 is arranged at the end of the inverted mountain-shaped prefabricated section 1 and the mountain-shaped prefabricated section 2, and the bellows 6 is arranged at the right angle between the inverted U-shaped prefabricated section 1 and the U-shaped prefabricated section 2 , the steel plate waterstop 7 is arranged inside the inverted U-shaped prefabricated section 1 and the U-shaped...
Embodiment 2
[0062] Such as Figure 5-9 As shown, the closed prefabricated section is a double-hole prefabricated section, which includes an inverted mountain-shaped prefabricated section 8, a mountain-shaped prefabricated section 9, a shear key 3, a shear keyway 4, a pre-embedded steel plate 5, a corrugated The pipe 6 and the steel plate waterstop 7, the lower end surface of the inverted mountain-shaped prefabricated section 8 and the upper end surface of the mountain-shaped prefabricated section 9 are matched and spliced, and the shear force key 3 and the shear force keyway 4 are used to cooperate at the splicing surface. The pre-embedded steel plate 5 is arranged at the end of the mountain-shaped prefabricated section 8 and the mountain-shaped prefabricated section 9, and the bellows 6 is arranged at the end of the mountain-shaped prefabricated section 8 and the mountain-shaped prefabricated section 9. At the right angle, the steel plate waterstop 76 is arranged inside the inverted moun...
PUM
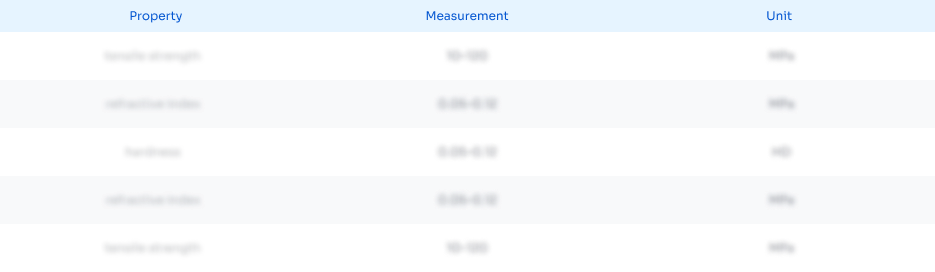
Abstract
Description
Claims
Application Information

- R&D Engineer
- R&D Manager
- IP Professional
- Industry Leading Data Capabilities
- Powerful AI technology
- Patent DNA Extraction
Browse by: Latest US Patents, China's latest patents, Technical Efficacy Thesaurus, Application Domain, Technology Topic, Popular Technical Reports.
© 2024 PatSnap. All rights reserved.Legal|Privacy policy|Modern Slavery Act Transparency Statement|Sitemap|About US| Contact US: help@patsnap.com