High-temperature resistant conductive polytetrafluoroethylene hot melting adhesive tape and production method thereof
A technology of polytetrafluoroethylene and polytetrafluoroethylene film, which is applied in the production of high-temperature-resistant conductive polytetrafluoroethylene hot-melt tape, and in the field of high-temperature-resistant conductive polytetrafluoroethylene hot-melt tape, which can solve the problem of low conductivity of hot-melt tape , Inconvenient replacement of filter material, restricted application and other problems, to achieve significant beneficial effects, improved scratch resistance, and improved charge transport capacity
- Summary
- Abstract
- Description
- Claims
- Application Information
AI Technical Summary
Problems solved by technology
Method used
Examples
Embodiment 1
[0046] Carry out the production of high-temperature-resistant conductive polytetrafluoroethylene hot-melt tape according to the following steps.
[0047] (1) Preparation of polytetrafluoroethylene film layer
[0048] First, fully mix 64g of polytetrafluoroethylene micropowder, 12g of liquid lubricant, 1g of conductive carbon black, 1g of metal particles, and 2g of carbon nanotubes, and let it stand for 3 hours at a temperature of 100°C to form a polytetrafluoroethylene material;
[0049] Then, the polytetrafluoroethylene material is pressed into a cylindrical blank by a compacting machine, and the pressing temperature is 50°C;
[0050] Finally, the cylindrical blank is extruded into a rod at 60°C by a pusher, and then rolled into a polytetrafluoroethylene film layer by a calender at 80°C;
[0051] (2) Preparation of polyethylene layer
[0052] Mix 60g of ethylene, 25g of softening oil, 5g of antioxidant, and 10g of functional filler to obtain polyethylene, and coat the obtai...
Embodiment 2
[0054] Carry out the production of high-temperature-resistant conductive polytetrafluoroethylene hot-melt tape according to the following steps.
[0055] (1) Preparation of polytetrafluoroethylene film layer
[0056] First, fully mix 70g of polytetrafluoroethylene micropowder, 22g of liquid lubricant, 3g of conductive carbon black, and 4g of carbon nanotubes, and let it stand for 8 hours at a temperature of 70°C to form a polytetrafluoroethylene material;
[0057] Then, the polytetrafluoroethylene material is pressed into a cylindrical blank by a compacting machine, and the pressing temperature is 30°C;
[0058] Finally, the cylindrical blank is extruded into a rod at 50°C by a pusher, and then rolled into a polytetrafluoroethylene film layer by a calender at 70°C;
[0059] (2) Preparation of polyethylene layer
[0060] Mix 70g of ethylene, 20g of softening oil, 4g of antioxidant, and 6g of functional filler to obtain polyethylene, and coat the prepared polyethylene on the PTF...
Embodiment 3
[0062] Carry out the production of high-temperature-resistant conductive polytetrafluoroethylene hot-melt tape according to the following steps.
[0063] (1) Preparation of polytetrafluoroethylene film layer
[0064] First, 82g of polytetrafluoroethylene micropowder, 19g of liquid lubricant, 4g of metal particles, and 5g of carbon nanotubes are fully mixed, and left to stand for 6 hours at a temperature of 80°C to form a polytetrafluoroethylene material;
[0065] Then, the polytetrafluoroethylene material is pressed into a cylindrical blank by a compacting machine, and the pressing temperature is 45°C;
[0066] Finally, the cylindrical blank is extruded into a rod at 45°C by a pusher, and then rolled into a polytetrafluoroethylene film layer by a calender at 50°C;
[0067] (2) Preparation of polyethylene layer
[0068] Mix 75g of ethylene, 15g of softening oil, 3g of antioxidant, and 7g of functional filler to polymerize to obtain polyethylene, and coat the prepared polyethy...
PUM
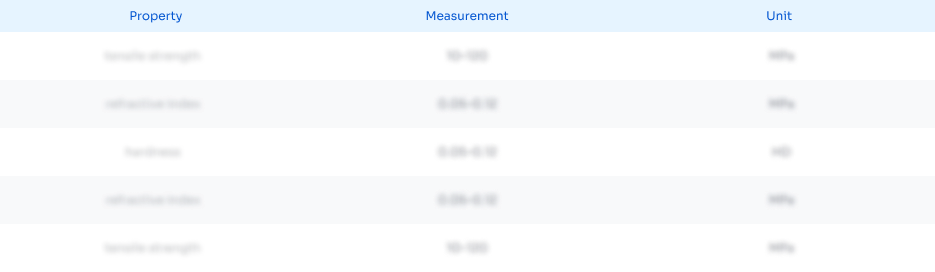
Abstract
Description
Claims
Application Information

- R&D
- Intellectual Property
- Life Sciences
- Materials
- Tech Scout
- Unparalleled Data Quality
- Higher Quality Content
- 60% Fewer Hallucinations
Browse by: Latest US Patents, China's latest patents, Technical Efficacy Thesaurus, Application Domain, Technology Topic, Popular Technical Reports.
© 2025 PatSnap. All rights reserved.Legal|Privacy policy|Modern Slavery Act Transparency Statement|Sitemap|About US| Contact US: help@patsnap.com