Clamp for disc-shaped large casting multi-hole and multi-plane finish machining
A large-scale casting, disc-shaped technology, used in manufacturing tools, workpiece clamping devices, metal processing equipment, etc., can solve the problems of unstable clamping, long processing time, inaccurate positioning accuracy, etc. The effect of machining dimensional accuracy, improving production and processing quality, and high clamping stability
- Summary
- Abstract
- Description
- Claims
- Application Information
AI Technical Summary
Problems solved by technology
Method used
Image
Examples
Embodiment Construction
[0019] In order to deepen the understanding of the present invention, the present invention will be further described below in conjunction with the accompanying drawings and embodiments, which are only used to explain the present invention and do not limit the protection scope of the present invention.
[0020] like figure 1 and image 3 As shown in the figure, the fixture for porous multi-plane finishing of disc-shaped large-scale castings includes a ring-shaped protrusion 3 arranged on a base 4, and a clamping disc 2 is connected to the top of the ring-shaped protrusion 3 through a rotating shaft 7, and the clamping The disc 2 is obliquely connected to the disc-shaped protrusion 3; several lower positioning pieces 6 are arranged between the clamping disc 2 and the disc-shaped protrusion 3, and several lower positioning pieces 6 are fixedly connected to the disc-shaped protrusion. 3, several upper positioning pieces 1 are also connected above the clamping disc 2, and several...
PUM
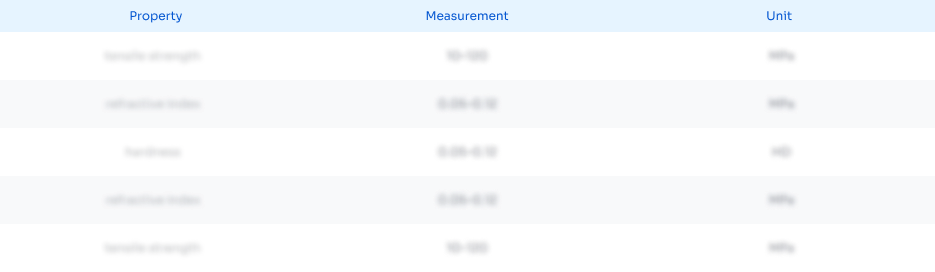
Abstract
Description
Claims
Application Information

- R&D
- Intellectual Property
- Life Sciences
- Materials
- Tech Scout
- Unparalleled Data Quality
- Higher Quality Content
- 60% Fewer Hallucinations
Browse by: Latest US Patents, China's latest patents, Technical Efficacy Thesaurus, Application Domain, Technology Topic, Popular Technical Reports.
© 2025 PatSnap. All rights reserved.Legal|Privacy policy|Modern Slavery Act Transparency Statement|Sitemap|About US| Contact US: help@patsnap.com