Device and method for improving magnetostrictive guided wave detection sensitivity
A technology of detection sensitivity and magnetostriction, which can be used in measurement devices, analysis of solids using sonic/ultrasonic/infrasonic waves, and material analysis using sonic/ultrasonic/infrasonic waves, etc. Achieve defect detection without blind spots, low cost of equipment improvement, and increase the effect of sound wave attenuation
- Summary
- Abstract
- Description
- Claims
- Application Information
AI Technical Summary
Problems solved by technology
Method used
Image
Examples
Embodiment 1
[0052] The pipeline to be tested is figure 2 As shown, point a to point d is a section of the pipeline to be detected with a length of 2m. Install the signal enhancement components at both ends of the area to be detected respectively, the excitation sensor is installed at point a close to the signal enhancement component at the left end, and the receiving sensor is installed at point b, and the distance from the signal enhancement component at the left end is L 1 , and other components are also connected in sequence; the distance between the defect and the receiving sensor is L 2 , the distance from the signal enhancement element at the right end is L 3 , then the amplitude of the first defect echo signal D1 can be expressed as
[0053] A 1 = A 0 · R D · e - α ( ...
Embodiment 2
[0062] image 3 It is a structural schematic diagram of a signal enhancement element for a tubular or rod-shaped object to be detected, including: an attenuation module 13 , a reflection module 15 , a partition 14 , and a housing 12 .
[0063] Wherein, the reflection module 15, the partition 14 and the attenuation module 13 jointly constitute the inner layer of the signal enhancement element 1, which is fixed on the outer surface of the object 5 to be detected by the outer shell, the material of the reflection module 15 is steel, and the material of the attenuation module 13 is rubber.
[0064] The reflection module 15 and the attenuation module 13 are arranged on the outer surface of the object to be detected 5, and three pairs of partitions 14 are respectively arranged between the reflection module 15 and the attenuation module 13, and at both ends of the inner layer of the signal enhancement element.
[0065] The attenuation module 13, the reflection module 15, the casing ...
Embodiment 3
[0067] Figure 4 According to the working schematic diagram of the device for improving the detection sensitivity of magnetostrictive guided waves according to the present invention, the detection object 5 is 25mm in outer diameter, 20mm in inner diameter, and the length is L 1 = 2.8m steel pipe, 0.5mm deep transverse groove defect 17 distance L from the left end of the pipe 2 =0.8m, the equivalent cross-sectional area loss is about 14.4%. Set L from the left end of the pipe 3 A section of =1.2m is the detection area. The device is equipped with a signal enhancement element 1 in Embodiment 2 at the right end of the detection area. The internal diameter of this element is 24mm, and its reflection module 15 is installed near the sensor 3 (4). The detection steps are as follows:
[0068] (1) The central processor controls the signal generator to generate an excitation signal, which is input to the excitation sensor 3 through a power amplifier, and is excited to generate an ult...
PUM
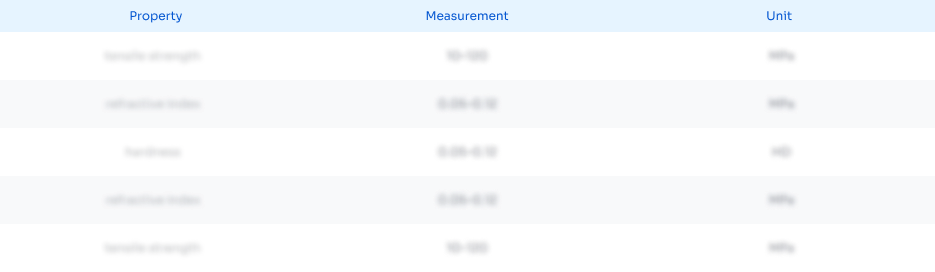
Abstract
Description
Claims
Application Information

- R&D Engineer
- R&D Manager
- IP Professional
- Industry Leading Data Capabilities
- Powerful AI technology
- Patent DNA Extraction
Browse by: Latest US Patents, China's latest patents, Technical Efficacy Thesaurus, Application Domain, Technology Topic, Popular Technical Reports.
© 2024 PatSnap. All rights reserved.Legal|Privacy policy|Modern Slavery Act Transparency Statement|Sitemap|About US| Contact US: help@patsnap.com