Corrugated paper core and honeycomb paper core cork surface layer composite board manufacturing processes
A technology of honeycomb paper core and manufacturing process, applied in the field of cork composite board, can solve the problems of slow production speed, low production speed, affecting product quality, etc., and achieve the effect of improving production efficiency, reducing production cost, and avoiding continuous production.
- Summary
- Abstract
- Description
- Claims
- Application Information
AI Technical Summary
Problems solved by technology
Method used
Image
Examples
Embodiment 1
[0021] Embodiment one: see figure 1 , 2 , a manufacturing process of a corrugated core cork composite board in the figure, comprising the following steps;
[0022] ①. Glue the cork coil and the paper coil through the gluing equipment, and wind up after gluing to form a flexible cork and paper composite coil; the paper used in this step is preferably kraft paper with good strength and toughness, and ordinary paper is also acceptable. As long as the strength and toughness are sufficient.
[0023] ②.Using the above-mentioned cork and paper composite coil as the surface layer paper for corrugated boxboard production, put it on the existing continuous production line of cartonboard, and glue and compound it with the corrugated paper core to make the surface layer into a cork layer with internal Corrugated composite board with a corrugated core.
[0024] Described step ② includes the following sub-steps
[0025] a. Unwind
[0026] Including corrugated paper core unwinding, cor...
Embodiment 2
[0034] Embodiment two: see figure 1 , 3 , a corrugated core cork composite board manufacturing process, comprising the following steps;
[0035] ①. Glue the cork coil and the paper coil through the gluing equipment, and wind up after gluing to form a flexible cork and paper composite coil; the paper used in this step is preferably kraft paper with good strength and toughness, and ordinary paper is also acceptable. As long as the strength and toughness are sufficient.
[0036] ②.Using the above-mentioned cork and paper composite coil as the surface layer paper for corrugated boxboard production, put it on the existing continuous production line of cartonboard, and glue and compound it with the corrugated paper core to make the surface layer into a cork layer with internal Corrugated composite board with a corrugated core.
[0037] Described step ② includes the following sub-steps
[0038] a. Unwind
[0039] Including corrugated paper core unwinding, cork and paper compos...
Embodiment 3
[0047] Embodiment three: see figure 1 , 4 . A manufacturing process of a corrugated core cork composite board, comprising the following steps;
[0048] ①. Glue the cork coil and the paper coil through the gluing equipment, and wind up after gluing to form a flexible cork and paper composite coil; the paper used in this step is preferably kraft paper with good strength and toughness, and ordinary paper is also acceptable. As long as the strength and toughness are sufficient.
[0049] ②.Using the above-mentioned cork and paper composite coil as the surface layer paper for corrugated boxboard production, put it on the existing continuous production line of cartonboard, and glue and compound it with the corrugated paper core to make the surface layer into a cork layer with internal Corrugated composite board with a corrugated core.
[0050] Described step ② includes the following sub-steps
[0051] a. Unwind
[0052] Including corrugated paper core unwinding, cork and paper ...
PUM
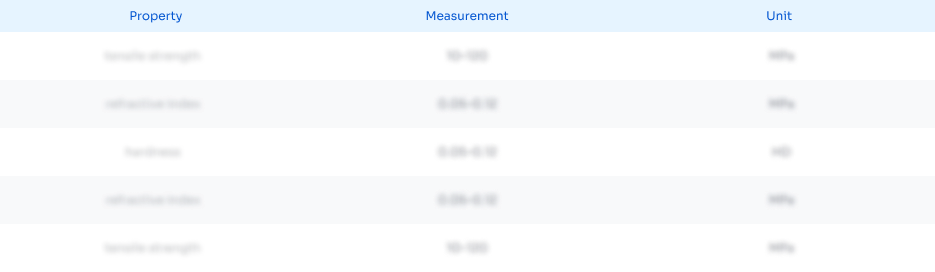
Abstract
Description
Claims
Application Information

- Generate Ideas
- Intellectual Property
- Life Sciences
- Materials
- Tech Scout
- Unparalleled Data Quality
- Higher Quality Content
- 60% Fewer Hallucinations
Browse by: Latest US Patents, China's latest patents, Technical Efficacy Thesaurus, Application Domain, Technology Topic, Popular Technical Reports.
© 2025 PatSnap. All rights reserved.Legal|Privacy policy|Modern Slavery Act Transparency Statement|Sitemap|About US| Contact US: help@patsnap.com