Carbon steel pipe welding technology
A welding process and pipeline technology, applied in the field of steel pipe welding, can solve the problems that the production volume cannot meet the market demand, weak welding mechanical performance, poor welding mechanical performance, etc., to avoid repeated welding, improve mechanical strength, welding solid effect
- Summary
- Abstract
- Description
- Claims
- Application Information
AI Technical Summary
Problems solved by technology
Method used
Image
Examples
Embodiment 1
[0021] Such as figure 1 As shown, the present invention includes a welding process for carbon steel pipelines, comprising the steps of:
[0022] A) Groove processing, the groove form and groove size of the pipe shall meet the requirements of the design documents or welding process card;
[0023] B) Assembling, prior to the assemblage of weldments, the paint, scale, burr and galvanized layer on the groove and its inner and outer surfaces shall be cleaned up. The edge amount is less than 10% of the pipe wall thickness;
[0024] C) Preheat the weldment group before welding, and the preheating temperature is between 100°C and 200°C;
[0025] D) Perform tack welding on the welded components after the first preheating, immediately remove the defective components after welding, reposition and then perform the second preheating before welding;
[0026] E) Carry out visual inspection of the welds on the welded components;
[0027] F) Perform welding heat treatment for the qualified...
Embodiment 2
[0031] This embodiment is preferably as follows on the basis of Embodiment 1: the material of the matching jig to be welded with the base metal during tack welding in step D) is the same type, and the base metal should not be damaged when the jig is removed. The remaining weld scars should be ground and repaired until the surface of the base metal is flush. The clamping tool made of this material has a higher degree of fit, which can further reduce the gap of virtual welding during the welding process and improve the mechanical strength of the weld.
[0032] In step C), the preheating width shall be based on the center of the weld, and each side shall not be less than 3 times the thickness of the weldment. Guarantee the quality of the weld.
[0033] In step E), argon tungsten arc welding is used for welding the carbon steel pipes in the welded assembly with a pipe diameter less than or equal to 60 mm, and argon tungsten arc welding is used for bottom welding and manual arc we...
PUM
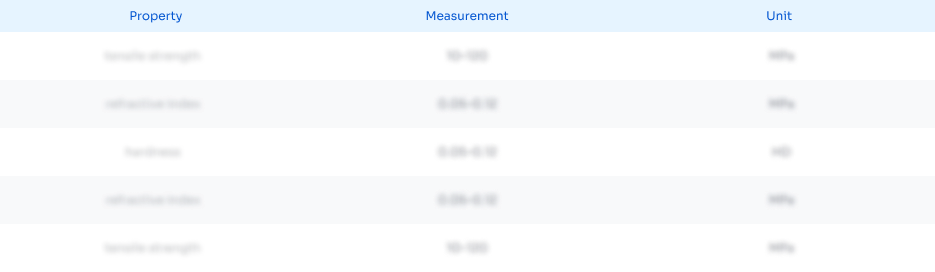
Abstract
Description
Claims
Application Information

- R&D
- Intellectual Property
- Life Sciences
- Materials
- Tech Scout
- Unparalleled Data Quality
- Higher Quality Content
- 60% Fewer Hallucinations
Browse by: Latest US Patents, China's latest patents, Technical Efficacy Thesaurus, Application Domain, Technology Topic, Popular Technical Reports.
© 2025 PatSnap. All rights reserved.Legal|Privacy policy|Modern Slavery Act Transparency Statement|Sitemap|About US| Contact US: help@patsnap.com