Production method of non-pulverized thick-specification zinc-iron alloyed plate
A zinc-iron alloy and production method technology, applied in metal material coating process, coating, hot-dip plating process, etc., can solve the problems of bright edge and high powdering level, so as to reduce production cost and solve the problem of coating powdering Effect
- Summary
- Abstract
- Description
- Claims
- Application Information
AI Technical Summary
Problems solved by technology
Method used
Image
Examples
Embodiment 1
[0037] 1) Annealing: Anneal the steel strip with a thickness of 2.0mm on the continuous production line. The temperature is 461°C.
[0038] 2) Galvanizing: the annealed steel strip is galvanized, the temperature of the zinc bath is controlled at 460°C, the aluminum content of the zinc bath is 0.13wt%, and the galvanizing time is 7 seconds. figure 1 .
[0039] 3) Alloying: The galvanized steel strip (that is, the galvanized sheet) enters the alloying furnace before the coating is solidified. The high-frequency induction power is set at 480KW, and the galvanized sheet is heated to 530°C within 5S, and then carried out Heat preservation, control the heat preservation time to 14s, and the heat preservation temperature to 420°C, to obtain the microscopic surface morphology of the alloyed plate see figure 2 .
[0040] 4) Leveling: The alloyed plate is leveled, using a leveling roll with a roughness Ra of 2.0, and the rolling force tonnage of the system is set to 200 tons to ens...
Embodiment 2
[0043] 1) Annealing: Anneal the strip steel with a thickness of 1.8mm on the continuous production line. The running speed on the continuous production line is 42m / min, the temperature of the preheating furnace is 650°C, the reduction annealing temperature is 735°C, and the temperature of the zinc pot is 462°C .
[0044] 2) Galvanizing: the annealed steel strip is galvanized, the temperature of the zinc solution is controlled at 460°C, the aluminum content of the zinc solution is 0.135wt%, and the galvanizing time is 6 seconds to obtain a galvanized sheet.
[0045] 3) Alloying: The galvanized steel strip (that is, the galvanized sheet) enters the alloying furnace before the coating is solidified. The high-frequency induction power is set at 510KW, and the galvanized sheet is heated to 520°C within 5S, and then carried out For heat preservation, the heat preservation time is controlled to be 13s, and the heat preservation temperature is 430°C to obtain an alloyed plate.
[004...
Embodiment 3
[0049] 1) Annealing: Anneal the strip steel with a thickness of 1.7mm on the continuous production line. The running speed of the strip steel on the continuous production line is 48m / min. The temperature is 463°C.
[0050] 2) Galvanizing: the annealed steel strip is galvanized, the temperature of the zinc solution is controlled at 462° C., the aluminum content of the zinc solution is 0.125 wt%, and the galvanizing time is 6 seconds to obtain a galvanized sheet.
[0051] 3) Alloying: The galvanized steel strip (that is, the galvanized sheet) enters the alloying furnace before the coating is solidified. The high-frequency induction power is set at 530KW, and the galvanized sheet is heated to 520°C within 5S, and then carried out For heat preservation, the heat preservation time is controlled to be 12s, and the heat preservation temperature is 440°C to obtain an alloyed plate.
[0052] 4) Leveling: The alloyed plate is leveled, using a leveling roll with a roughness Ra of 2.0, a...
PUM
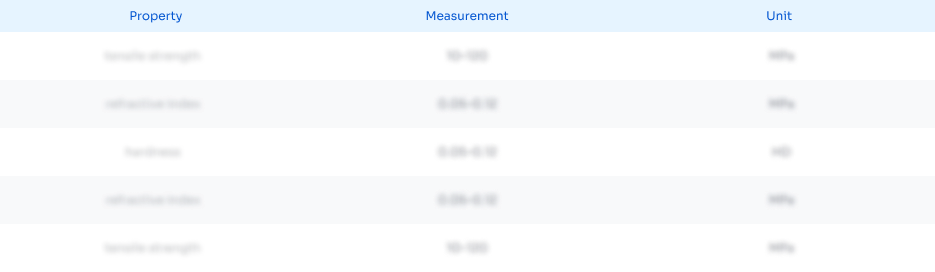
Abstract
Description
Claims
Application Information

- Generate Ideas
- Intellectual Property
- Life Sciences
- Materials
- Tech Scout
- Unparalleled Data Quality
- Higher Quality Content
- 60% Fewer Hallucinations
Browse by: Latest US Patents, China's latest patents, Technical Efficacy Thesaurus, Application Domain, Technology Topic, Popular Technical Reports.
© 2025 PatSnap. All rights reserved.Legal|Privacy policy|Modern Slavery Act Transparency Statement|Sitemap|About US| Contact US: help@patsnap.com