Worm grinding wheel gear grinding surface distortion compensation method
A technology of worm grinding wheel and compensation method, which is applied in the direction of gear teeth, worms, gear teeth manufacturing devices, etc., and can solve the problem of high requirements for machine tools
- Summary
- Abstract
- Description
- Claims
- Application Information
AI Technical Summary
Problems solved by technology
Method used
Image
Examples
Embodiment Construction
[0046] The present invention will be described in further detail below in conjunction with the accompanying drawings and specific embodiments.
[0047] According to the present invention, the diamond roller wheel used to dress the worm grinding wheel should include two movements of rotation and deflection according to the requirements, and the position of the rotation axis of the roller should be at the front end of the deflection axis. Its specific structure is as follows: figure 1 shown. In the figure, 1 represents the deflection axis of the roller, 2 represents the rotation axis of the roller, 3 represents the diamond roller, and 4 represents the pitch line of the roller.
[0048] The grinding process of worm grinding wheel is generally divided into rough grinding and fine grinding, and the grinding allowance of rough grinding is greater than that of fine grinding. Therefore, the worm grinding wheel is divided into rough grinding area, fine grinding area and intermediate tr...
PUM
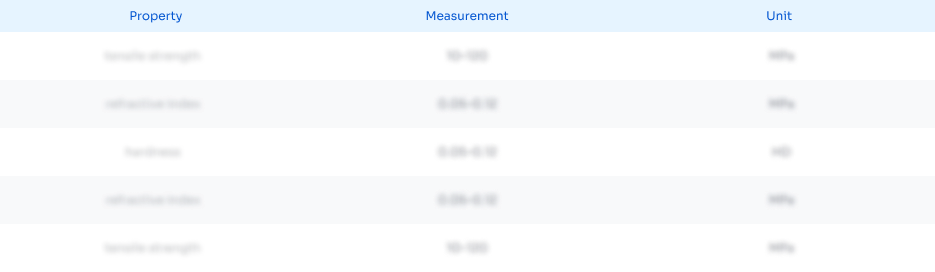
Abstract
Description
Claims
Application Information

- R&D Engineer
- R&D Manager
- IP Professional
- Industry Leading Data Capabilities
- Powerful AI technology
- Patent DNA Extraction
Browse by: Latest US Patents, China's latest patents, Technical Efficacy Thesaurus, Application Domain, Technology Topic, Popular Technical Reports.
© 2024 PatSnap. All rights reserved.Legal|Privacy policy|Modern Slavery Act Transparency Statement|Sitemap|About US| Contact US: help@patsnap.com