Time-based sheet forming limit determination method
A method for determining the forming limit and a technology for determining the forming limit, which is applied in the field of time-based determination of the forming limit of thin plates, which can solve the problems such as the failure to accurately control the stop of the sample, the failure of the rupture point to fully reflect the in-situ deformation of the inspection point, and the inability to truly determine the limit strain.
- Summary
- Abstract
- Description
- Claims
- Application Information
AI Technical Summary
Problems solved by technology
Method used
Image
Examples
Embodiment 1
[0017] see figure 2 , a time-based thin plate forming limit determination method provided by an embodiment of the present invention includes:
[0018] Step 110: set up a steel ball mold bulging test;
[0019] Step 120: Carry out the steel ball mold bulging test to the plate, and take pictures of the bulging sample until the plate breaks;
[0020] Step 130: Obtain the previous frame image of the sample just cracking according to the photograph taken, take the cracking point as the center, select an area near the cracking point as the investigation area;
[0021] Step 140: obtain the surface principal strain average value and the surface secondary strain average value of the investigation area;
[0022] Step 150: According to the principle of constant volume, calculate the principal strain in the thickness direction and the strain rate in the thickness direction;
[0023] Step 160: Obtain the data of the stable stage and the unstable stage according to the thickness strain r...
Embodiment 2
[0037] In order to introduce the embodiment of the present invention more clearly, the following will introduce it from the specific examples of the embodiment of the present invention.
specific Embodiment 1
[0038] The steel ball die bulging in GB / T 15825.8-2008 Forming Limit Diagram Determination Method is used for the test, and a high-frequency camera is used to take pictures of the bulging sample until the material breaks. The image collection of each sample during the deformation process is not less than 50 photos, and the image collection can also be concentrated in the late stage of sample deformation, in order to increase the sampling frequency of the sample at the end of deformation.
[0039] Find out the position of the sample rupture point, and retrieve the image in reverse order of time to obtain the previous frame image of the sample just before the rupture point, and select several areas close to the rupture point with the rupture point as the center. The number of selected areas depends on the resolution of the camera and the electronic grid size of the software.
[0040] For each photo, use the strain analysis software to analyze the average value of the surface pri...
PUM
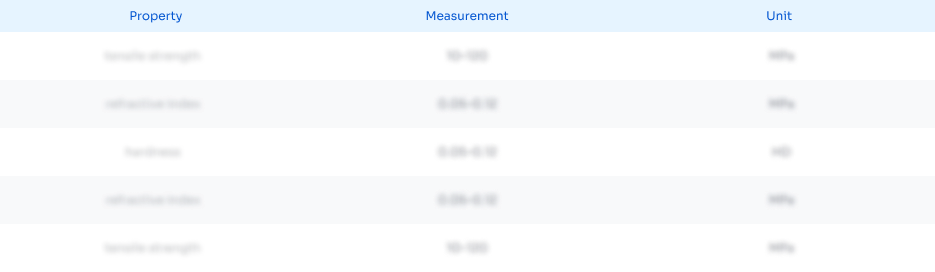
Abstract
Description
Claims
Application Information

- R&D
- Intellectual Property
- Life Sciences
- Materials
- Tech Scout
- Unparalleled Data Quality
- Higher Quality Content
- 60% Fewer Hallucinations
Browse by: Latest US Patents, China's latest patents, Technical Efficacy Thesaurus, Application Domain, Technology Topic, Popular Technical Reports.
© 2025 PatSnap. All rights reserved.Legal|Privacy policy|Modern Slavery Act Transparency Statement|Sitemap|About US| Contact US: help@patsnap.com