Splash-proof device for vacuum melting
A vacuum smelting and splash-proof technology, applied in the field of precision casting, can solve the problems of no thermal insulation feeding effect, affecting the product qualification rate, uneconomical metal film covering method, etc., and achieve the goals of reducing production costs, convenient operation and improving product quality Effect
- Summary
- Abstract
- Description
- Claims
- Application Information
AI Technical Summary
Problems solved by technology
Method used
Image
Examples
Embodiment Construction
[0008] The specific embodiments of the present invention will be further described below in conjunction with the accompanying drawings.
[0009] figure 1 As shown, the present invention is a splash-proof device for vacuum smelting. The sealing sleeve 2 is arranged on one side of the vacuum furnace wall 1, the curved rod 3 is arranged in the sealing sleeve 2, and the splash-proof cover 6 is arranged inside the curved rod 3. On the end, the bimetal claw 8 is connected under the splash-proof cover 6, the heat preservation cover 7 is set in the bimetal claw 8, the upper end of the connecting rod 4 is connected with the outer end of the curved rod 3, and the lower end of the connecting rod 4 is connected with the vacuum furnace Pedal 5 on the connection.
[0010] In the present invention, the pedal arranged on the vacuum furnace is connected with the lower end of the connecting rod, so that the switch of the splash-proof cover is convenient to operate; the double-metal claws arran...
PUM
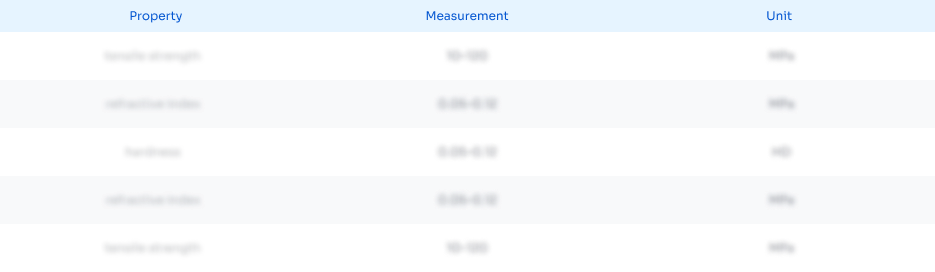
Abstract
Description
Claims
Application Information

- R&D
- Intellectual Property
- Life Sciences
- Materials
- Tech Scout
- Unparalleled Data Quality
- Higher Quality Content
- 60% Fewer Hallucinations
Browse by: Latest US Patents, China's latest patents, Technical Efficacy Thesaurus, Application Domain, Technology Topic, Popular Technical Reports.
© 2025 PatSnap. All rights reserved.Legal|Privacy policy|Modern Slavery Act Transparency Statement|Sitemap|About US| Contact US: help@patsnap.com