Control method of cleanliness of interstitial-free steel
A technology of interstitial atom-free steel and control method, applied in the direction of manufacturing converters, etc., can solve the problems of deteriorating the cleanliness of molten steel, and achieve the effect of improving the cleanliness of molten steel, reducing the generation of inclusions, and ensuring the cleanliness.
- Summary
- Abstract
- Description
- Claims
- Application Information
AI Technical Summary
Problems solved by technology
Method used
Image
Examples
Embodiment 1
[0051] S1: Put the desulfurized molten iron into the dephosphorization converter and the decarburization converter for dual smelting. The end target of controlled decarburization converter blowing is O: 0.098%, C: 0.022%, and the end temperature is 1689°C. The steel is tapped directly at the end of the converter without deoxidation to obtain the first molten steel. During the tapping process, 400kg of small-grained lime and 160kg of slow-release deoxidizer are added to carry out slag modification. During the tapping process, slag blocking is used to tap the steel, and the slag thickness is controlled to 75mm.
[0052] S2: RH refining is performed on the first molten steel. The target temperature of RH refining is 1632℃, the carbon content is 0.022%, and the oxygen content is 0.085%. If the actual arrival temperature deviates from the target arrival temperature by more than 15°C, use cooling scrap steel or OB to blow oxygen to perform temperature compensation operation. For ...
Embodiment 2
[0055] S1: Put the desulfurized molten iron into the dephosphorization converter and the decarburization converter for dual smelting. The end target of controlled decarburization converter blowing is O: 0.0823%, C: 0.037%, and the end temperature is 1689°C. The steel is tapped directly at the end of the converter without deoxidation to obtain the first molten steel. During the tapping process, 400kg of small-grained lime and 130kg of slow-release deoxidizer are added for slag modification. During the tapping process, slag blocking is used to control the slag thickness to 80mm.
[0056] S2: RH refining is performed on the first molten steel. The target temperature of the RH refining station is 1627°C, the carbon content is 0.027%, and the oxygen content is 0.072%. If the actual arrival temperature deviates from the target arrival temperature by more than 15°C, use cooling scrap steel or OB to blow oxygen to perform temperature compensation operation. For the molten steel ent...
Embodiment 3
[0059] S1: Put the desulfurized molten iron into the dephosphorization converter and the decarburization converter for dual smelting. The end target of controlled decarburization converter blowing is O: 0.084%, C: 0.026%, and the end temperature is 1685°C. The steel is tapped directly at the end of the converter without deoxidation to obtain the first molten steel. During the tapping process, 400kg of small-grained lime and 130kg of slow-release deoxidizer are added for slag modification. During the tapping process, slag blocking is used to control the slag thickness to 70mm.
[0060] S2: RH refining is performed on the first molten steel. The target temperature of RH refining is 1627℃, the carbon content is 0.026%, and the oxygen content is 0.077%. If the actual arrival temperature deviates from the target arrival temperature by more than 15°C, use cooling scrap steel or OB to blow oxygen to perform temperature compensation operation. For the molten steel entering the stat...
PUM
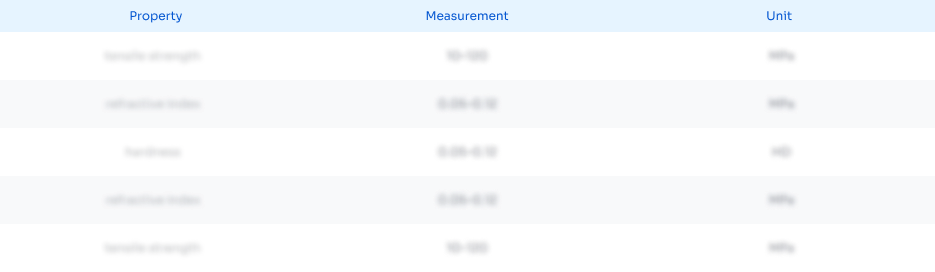
Abstract
Description
Claims
Application Information

- Generate Ideas
- Intellectual Property
- Life Sciences
- Materials
- Tech Scout
- Unparalleled Data Quality
- Higher Quality Content
- 60% Fewer Hallucinations
Browse by: Latest US Patents, China's latest patents, Technical Efficacy Thesaurus, Application Domain, Technology Topic, Popular Technical Reports.
© 2025 PatSnap. All rights reserved.Legal|Privacy policy|Modern Slavery Act Transparency Statement|Sitemap|About US| Contact US: help@patsnap.com