An in situ growth of Si inside 2D carbon felt 3 no 4 nanowire approach
An in-situ growth, nanowire technology, applied in nanotechnology, nanotechnology, chemical instruments and methods, etc., can solve the problem of inability to grow uniform carbon felt, achieve controllable distribution density, overcome poor permeability, and improve the enhancement effect. Effect
- Summary
- Abstract
- Description
- Claims
- Application Information
AI Technical Summary
Problems solved by technology
Method used
Image
Examples
Embodiment 1
[0026] 1) Set the density to 0.2g / cm 3 The 2D carbon felt is processed into a cuboid with a size of 40mm×30mm×10mm, and ultrasonically cleaned twice in alcohol solution, each time for 15min;
[0027] 2) Load ferrocene catalyst in 2D carbon felt: impregnate the carbon felt with xylene supersaturated solution of ferrocene (mass fraction of ferrocene is about 15%) for 1 h, take it out and dry it in a drying oven;
[0028] 3) Dilute polysilazane with xylene: prepare a mixed solution of polysilazane and xylene with a volume fraction of polysilazane of 10%, and stir it magnetically for 1 hour;
[0029] 4) Immerse the carbon felt prepared in step 2 in the mixed solution of step 3, and quickly put it into a vacuum impregnation box for immersion until the xylene in the mixed solution is blotted dry;
[0030] 5) Put the carbon felt in step 4 into a horizontal tube furnace for heat treatment: raise the temperature from room temperature to 1450°C at a rate of 6°C / min, keep it warm for 4 ...
Embodiment 2
[0032] 1) Set the density to 0.48g / cm 3 The 2D carbon felt is processed into a cuboid with a size of 40mm×30mm×10mm, and ultrasonically cleaned twice in alcohol solution, each time for 15min;
[0033] 2) Load ferrocene catalyst in 2D carbon felt: impregnate the carbon felt with xylene supersaturated solution of ferrocene (mass fraction of ferrocene is about 15%) for 1 h, take it out and dry it in a drying oven;
[0034] 3) Diluting polysilazane with xylene: prepare a mixed solution of polysilazane and xylene with a volume fraction of polysilazane of 15%, and magnetically stir for 1 hour;
[0035] 4) Immerse the carbon felt prepared in step 2 in the mixed solution of step 3, and quickly put it into a vacuum impregnation box for immersion until the xylene in the mixed solution is blotted dry;
[0036]5) Put the carbon felt in step 4 into a horizontal tube furnace for heat treatment: raise the temperature from room temperature to 1550°C at a rate of 6°C / min, keep it warm for 5 h...
Embodiment 3
[0038] 1) Set the density to 0.45g / cm 3 The 2D carbon felt is processed into a cuboid with a size of 40mm×30mm×10mm, and ultrasonically cleaned twice in alcohol solution, each time for 15min;
[0039] 2) Loading the ferrocene catalyst in the 2D carbon felt: impregnate the carbon felt with a xylene supersaturated solution of ferrocene (the mass fraction of ferrocene is about 15%) for 1 hour, take it out and dry it in a drying oven;
[0040] 3) Dilute polysilazane with xylene: prepare a mixed solution of polysilazane and xylene with a volume fraction of polysilazane of 18%, and magnetically stir for 1 hour;
[0041] 4) Immerse the carbon felt prepared in step 2 in the mixed solution of step 3, and quickly put it into a vacuum impregnation box for immersion until the xylene in the mixed solution is blotted dry;
[0042] Put the carbon felt in step 4 into a horizontal tube furnace for heat treatment: raise the temperature from room temperature to 1650°C at a rate of 6°C / min, keep...
PUM
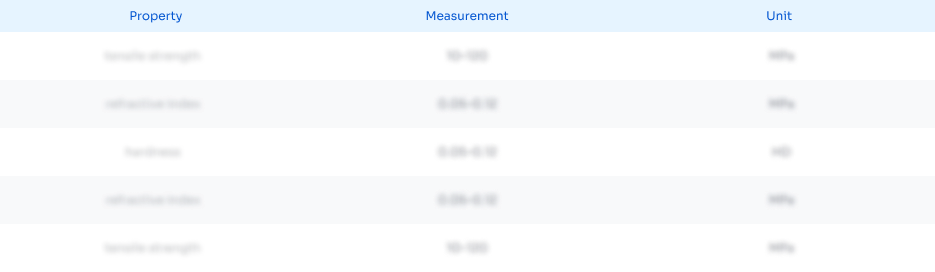
Abstract
Description
Claims
Application Information

- R&D
- Intellectual Property
- Life Sciences
- Materials
- Tech Scout
- Unparalleled Data Quality
- Higher Quality Content
- 60% Fewer Hallucinations
Browse by: Latest US Patents, China's latest patents, Technical Efficacy Thesaurus, Application Domain, Technology Topic, Popular Technical Reports.
© 2025 PatSnap. All rights reserved.Legal|Privacy policy|Modern Slavery Act Transparency Statement|Sitemap|About US| Contact US: help@patsnap.com