A process of preparing dimethyl carbonate by oxidative carbonylation of methanol
A technology for the oxidation of dimethyl carbonate and methanol, which is applied in the purification/separation of carbonate/haloformate, the preparation of organic compounds, the preparation of carbonate/haloformate, etc., and can solve the reaction and separation process Complexity and other problems, to achieve the effect of simplifying the reaction and separation process, improving the service life and small investment
- Summary
- Abstract
- Description
- Claims
- Application Information
AI Technical Summary
Problems solved by technology
Method used
Image
Examples
Embodiment 1
[0023] The inner diameter of the catalytic distillation tower is 80mm. The upper part of the catalytic distillation tower is the rectification section, the middle part is the reaction section, and the lower part is the stripping section. The bottom of the stripping section is equipped with a reboiler, and the top of the rectification section is equipped with a condenser and a buffer tank. . The reaction section is randomly packed with CuY catalyst formed into Raschig rings, with a height of 2800mm. The rectification section and stripping section are packed with ordinary separation packing stainless steel θ rings, the heights are respectively 200mm and 1000mm. After the catalytic distillation tower device is ready for purging and solid gas replacement, liquid methanol is fed from the top of the reaction section of the catalytic distillation tower at a space velocity of 0.2h -1 , CO and nitrogen are fed from the bottom of the stripping section, O 2 It is divided into 4 feeds in th...
Embodiment 2-10
[0024] Example 2-10: On the basis of the operation of Example 1, the filling height of each section of the catalytic distillation tower, the inner diameter of the tower, the type of packing, the type of catalyst, composition and molding, and the reaction operating conditions were changed. The specific catalytic distillation column parameters are shown in Table 1, the specific catalyst composition and preparation method are shown in Table 2, and the specific process conditions and reaction results are shown in Table 3.
[0025] Table 1
[0026]
[0027] Table 2
[0028]
[0029] table 3
[0030]
PUM
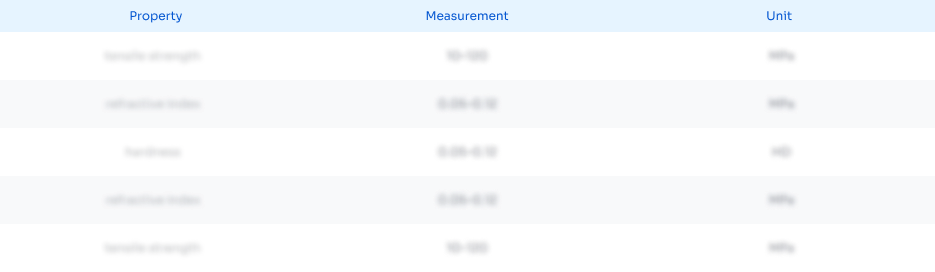
Abstract
Description
Claims
Application Information

- R&D
- Intellectual Property
- Life Sciences
- Materials
- Tech Scout
- Unparalleled Data Quality
- Higher Quality Content
- 60% Fewer Hallucinations
Browse by: Latest US Patents, China's latest patents, Technical Efficacy Thesaurus, Application Domain, Technology Topic, Popular Technical Reports.
© 2025 PatSnap. All rights reserved.Legal|Privacy policy|Modern Slavery Act Transparency Statement|Sitemap|About US| Contact US: help@patsnap.com