Method for recovering rare earth from rare earth-containing wastewater
A rare earth and waste water technology, which is applied in the direction of improving process efficiency, can solve the problems of poor thermal stability of catalytic cracking catalysts, high investment costs, and high organic content, and achieve obvious economic benefits and environmental protection benefits. The recovery process is simple, The effect of high recovery rate of rare earth
- Summary
- Abstract
- Description
- Claims
- Application Information
AI Technical Summary
Problems solved by technology
Method used
Examples
Embodiment 1
[0038] (1) Take 300g of rare earth-containing molecular sieve production wastewater (among them, RECl 3 The content is 0.1212g, wherein the rare earth metal elements, La accounts for 43% by weight, Ce accounts for 57% by weight) and 0.1213g of NaHCO 3 with Na 2 CO 3 mixture (Na 2 CO 3 with NaHCO 3 The weight ratio is 1:1), the reaction is carried out at a pH value of 7.5 and normal temperature (20°C), the reaction time is 20 minutes, solid-liquid separation is carried out after sedimentation for 120 minutes, and the rare earth precipitate and the first solution are obtained;
[0039](2) Add the obtained rare earth precipitate to 500g of a mixed aqueous solution of hydrofluoric acid HF and HCl (the weight ratio of HF and HCl is 4.4:1), and the molar ratio of hydrofluoric acid to rare earth metal elements is 1:0.25, The pH value of the solution is 2.5, react for 20 minutes, and settle for 120 minutes to separate the solid and liquid to obtain the rare earth fluoride and the...
Embodiment 2
[0042] (1) Take 500g of rare earth-containing molecular sieve production wastewater (among them, RECl 3 The content is 0.1868g, wherein the rare earth metal elements, La accounts for 43% by weight, Ce accounts for 57% by weight) and 0.2413g of NaHCO 3 with Na 2 CO 3 mixture (Na 2 CO 3 with NaHCO 3 The weight ratio is 1:2), the reaction is carried out at pH 8.5 and normal temperature (20°C), the reaction time is 30 minutes, the solid-liquid separation is carried out after 180 minutes of sedimentation, and the rare earth precipitate and the first solution are obtained;
[0043] (2) Add the obtained rare earth precipitate to 300g of a mixed aqueous solution of hydrofluoric acid HF and HCl (the weight ratio of HF and HCl is 1.6:1), and the molar ratio of hydrofluoric acid to rare earth metal elements is 1:0.2, The pH value of the solution is 2, react for 30 minutes, and settle for 180 minutes to separate the solid and liquid to obtain the rare earth fluoride and the second so...
Embodiment 3
[0046] (1) Take 400g of rare earth-containing molecular sieve production wastewater (among them, RECl 3 The content is 0.1348g, wherein the rare earth metal elements, La accounts for 43% by weight, Ce accounts for 57% by weight) and 0.1863g of NaHCO 3 with Na 2 CO 3 mixture (Na 2 CO 3 with NaHCO 3 The weight ratio is 1:3), the reaction is carried out at a pH value of 8 and normal temperature (20°C), the reaction time is 10 minutes, solid-liquid separation is carried out after 30 minutes of sedimentation, and the rare earth precipitate and the first solution are obtained;
[0047] (2) Add the obtained rare earth precipitate to 1000g of a mixed aqueous solution of hydrofluoric acid HF and HCl (the weight ratio of HF and HCl is 2.7:1), and the molar ratio of hydrofluoric acid to rare earth metal elements is 1:0.1, The pH value of the solution is 2.7, react for 10 minutes, and settle for 30 minutes to separate the solid and liquid to obtain the rare earth fluoride and the sec...
PUM
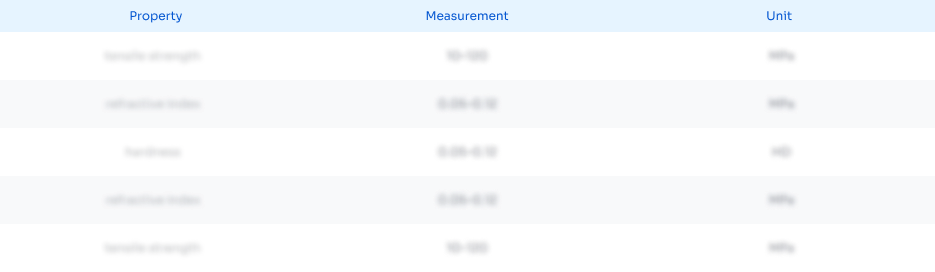
Abstract
Description
Claims
Application Information

- Generate Ideas
- Intellectual Property
- Life Sciences
- Materials
- Tech Scout
- Unparalleled Data Quality
- Higher Quality Content
- 60% Fewer Hallucinations
Browse by: Latest US Patents, China's latest patents, Technical Efficacy Thesaurus, Application Domain, Technology Topic, Popular Technical Reports.
© 2025 PatSnap. All rights reserved.Legal|Privacy policy|Modern Slavery Act Transparency Statement|Sitemap|About US| Contact US: help@patsnap.com