Low-pressure casting method for thin-walled aluminum alloy parts
A low-pressure casting, aluminum alloy technology, applied in the field of aluminum casting, can solve the problem of difficult to meet the tensile and deformation resistance of thin-walled aluminum parts
- Summary
- Abstract
- Description
- Claims
- Application Information
AI Technical Summary
Problems solved by technology
Method used
Image
Examples
Embodiment approach
[0011] The first step is to apply heat-conducting lubricating paint on the inner wall of the mold cavity and the riser:
[0012] Spray the thermal conductive paint colloid on the inner wall of the mold cavity and the liquid riser first, and then spray zinc oxide,
[0013] The riser pipe connects the mold cavity with the melting furnace;
[0014] The second step is to preheat the mold cavity and melt the aluminum alloy:
[0015] Use thermocouples to heat the mold, and control the temperature of the mold cavity at 250-350°C,
[0016] First use the melting furnace to heat and melt the 7A55 aluminum alloy. After the alloy is completely melted, then raise the melt temperature to 680-700°C to remove the slag on the surface, and finally raise the melt temperature to 710-720°C for the aluminum alloy melt to refine
[0017] The third step is gas replacement in the smelting furnace:
[0018] Introduce helium gas with a pressure of 0.01MPa into the melting furnace through the gas flo...
Embodiment 1
[0031] In Example 1, the mechanical properties of the thin-walled aluminum alloy casting obtained by controlling the mold cavity temperature at 255° C. in the second step and controlling the pouring pressure difference in the sixth step at 0.025 MPa in the above embodiment are as follows.
[0032]
Embodiment 2
[0033] In Example 2, the mechanical properties of the thin-walled aluminum alloy casting obtained by controlling the mold cavity temperature at 298° C. in the second step and controlling the pouring pressure difference in the sixth step at 0.03 MPa in the above embodiment are as follows.
[0034]
PUM
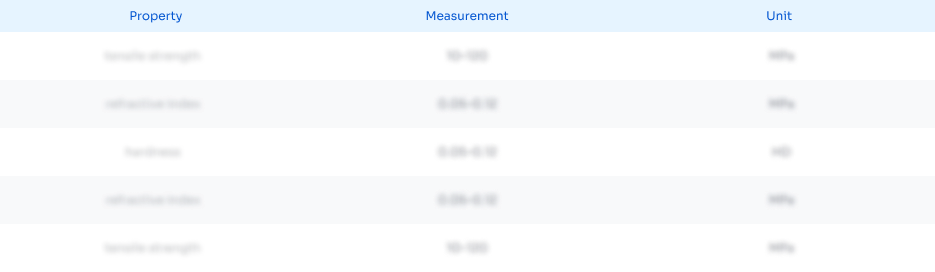
Abstract
Description
Claims
Application Information

- R&D Engineer
- R&D Manager
- IP Professional
- Industry Leading Data Capabilities
- Powerful AI technology
- Patent DNA Extraction
Browse by: Latest US Patents, China's latest patents, Technical Efficacy Thesaurus, Application Domain, Technology Topic, Popular Technical Reports.
© 2024 PatSnap. All rights reserved.Legal|Privacy policy|Modern Slavery Act Transparency Statement|Sitemap|About US| Contact US: help@patsnap.com