Lost foam casting method
A lost foam casting and white mold technology, which is applied to casting molding equipment, molds, mold components, etc., can solve the problems of short processing cycle and sand box collapse, achieve mechanical properties enhancement, eliminate residual stress, and save production. cost effect
- Summary
- Abstract
- Description
- Claims
- Application Information
AI Technical Summary
Problems solved by technology
Method used
Examples
Embodiment 1
[0047] Step 1: Make a foam plastic white mold, specifically follow the steps below:
[0048] Step 1.1: pre-foaming EPS beads;
[0049] Step 1.2: Place the EPS beads pre-foamed in step 1.1 in the curing chamber for curing, and the curing time is 4 hours;
[0050] Step 1.3: Fill the matured EPS beads in step 1.2 into the cavity of the metal mold, heat, expand and fuse with each other to form a white foam mold;
[0051] Step 2: Dry the foam plastic white mold made in step 1. The specific method of drying is: first place the foam plastic white mold at room temperature for 3 days, then place it in a drying room for 4 days, The temperature of the drying room is 20°C and the humidity is 10%;
[0052] Step 3: Repair and form the white foam mold after drying in step 2 to form a model cluster. Use the special stick glue for lost foam and the matching stick glue gun when assembling the shape;
[0053] Step 4: carry out hang coating to the model cluster formed in step 3;
[0054] Step...
Embodiment 2
[0063] Step 1: Make a foam plastic white mold, specifically follow the steps below:
[0064] Step 1.1: pre-foaming EPS beads;
[0065] Step 1.2: Place the EPS beads pre-foamed in step 1.1 in the curing chamber for curing, and the curing time is 20 hours;
[0066] Step 1.3: Fill the matured EPS beads in step 1.2 into the cavity of the metal mold, heat, expand and fuse with each other to form a white foam mold;
[0067] Step 2: Dry the foam plastic white mold made in step 1. The specific method of drying is: first place the foam plastic white mold at room temperature for 4 days, then put it in a drying room for 5 days, The temperature of the drying room is 30°C and the humidity is 30%;
[0068] Step 3: Repair and form the white foam mold after drying in step 2 to form a model cluster. Use the special stick glue for lost foam and the matching stick glue gun when assembling the shape;
[0069] Step 4: carry out hang coating to the model cluster formed in step 3;
[0070] Step ...
Embodiment 3
[0079] Step 1: Make a foam plastic white mold, specifically follow the steps below:
[0080] Step 1.1: pre-foaming EPS beads;
[0081] Step 1.2: Place the EPS beads pre-foamed in step 1.1 in the curing chamber for curing, and the curing time is 48 hours;
[0082] Step 1.3: Fill the matured EPS beads in step 1.2 into the cavity of the metal mold, heat, expand and fuse with each other to form a white foam mold;
[0083] Step 2: Dry the foam plastic white mold made in step 1. The specific method of drying is: first place the foam plastic white mold at room temperature for 5 days, then put it in a drying room for 3 days, The temperature of the drying room is 50°C and the humidity is 50%;
[0084] Step 3: Repair and form the white foam mold after drying in step 2 to form a model cluster. Use the special stick glue for lost foam and the matching stick glue gun when assembling the shape;
[0085] Step 4: carry out hang coating to the model cluster formed in step 3;
[0086] Step ...
PUM
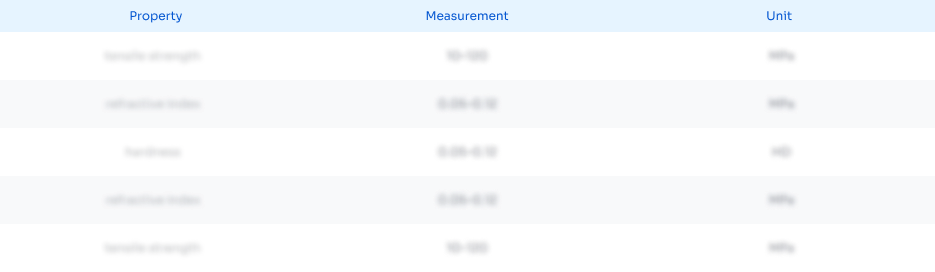
Abstract
Description
Claims
Application Information

- R&D
- Intellectual Property
- Life Sciences
- Materials
- Tech Scout
- Unparalleled Data Quality
- Higher Quality Content
- 60% Fewer Hallucinations
Browse by: Latest US Patents, China's latest patents, Technical Efficacy Thesaurus, Application Domain, Technology Topic, Popular Technical Reports.
© 2025 PatSnap. All rights reserved.Legal|Privacy policy|Modern Slavery Act Transparency Statement|Sitemap|About US| Contact US: help@patsnap.com