Leaching and recycling method for metals in anode waste materials of lithium-ion batteries
A technology for lithium-ion batteries and cathode materials, which is applied in the field of leaching metals from lithium-ion battery cathode waste, can solve the problems of lack of recovery technology for cathode waste and mixed cathode waste, and the failure to realize closed-loop circulation of metal components, etc., to achieve a wide range of applications , The leaching time is short, and the effect of avoiding secondary pollution
- Summary
- Abstract
- Description
- Claims
- Application Information
AI Technical Summary
Problems solved by technology
Method used
Image
Examples
Embodiment 1
[0101] The specific steps of the recycling method of lithium ion battery cathode waste based on metal closed-loop cycle are as follows:
[0102] (1) Take 30g of positive electrode waste generated in the production process of lithium-ion battery ternary composite positive electrode material nickel cobalt lithium manganate, first cut it into positive electrode waste fragments of about 10mm × 10mm, and then place these fragments in a drying oven at 65°C Dry at a constant temperature for 24 h, and measure the composition and content of metal elements in the dried cathode waste. The results are shown in Table 1.
[0103] Table 1 The mass percentage of metals in the dried nickel-cobalt lithium manganate cathode waste
[0104] Metal
Ni
Co
Mn
Li
Al
Mass content (wt.%)
18.32
18.65
17.57
6.15
7.86
[0105] (2) respectively take 9 parts of the dried positive waste scraps obtained by step (1) with a mass of about 2.5g, respe...
Embodiment 2
[0115] The specific steps of the recycling method of lithium ion battery cathode waste based on metal closed-loop cycle are as follows:
[0116] (1) Respectively take the lithium cobalt oxide (LiCoO) separated from the lithium ion battery 2 ) positive electrode waste 10g and lithium nickel manganate (LiNi 1 / 2 Mn 1 / 2 O 2 ) 20g of positive electrode waste, their size is about 5mm~15mm×5mm~15mm, mix them evenly and dry them at a constant temperature in a drying oven at 130°C for 12h to obtain a dried mixed positive electrode waste, measure the metal in the dried mixed positive electrode waste The composition and content of the elements are shown in Table 3.
[0117] Table 3 The mass percentage of metals in the mixed cathode waste after drying
[0118] Metal
Ni
Co
Mn
Li
Al
Mass content (wt.%)
19.21
17.83
18.92
6.95
10.71
[0119] (2) respectively get 9 parts of the mixed positive waste waste after drying obtained...
Embodiment 3
[0128] The specific steps of the recycling method of lithium ion battery cathode waste based on metal closed-loop cycle are as follows:
[0129] (1) Take the nickel-cobalt lithium manganate (LiNi) separated from the lithium-ion battery. x Co y Mn l–x–y O 2 ) Positive electrode waste 30g, the size is about 10mm × 15mm, dried at a constant temperature in a 200 ℃ drying oven for 6h, to obtain a dried mixed positive electrode waste, measure the composition and content of metals in the dried mixed positive electrode waste, and the results are shown in Table 5. Show.
[0130] Table 5 The mass percentage of metals in the mixed cathode waste after drying
[0131] Metal
Ni
Co
Mn
Li
Al
Mass content (wt.%)
20.13
18.79
19.25
7.03
8.22
[0132] (2) Take the dried positive waste material obtained by step (1) with a mass of about 2.0 g and add it to a conical flask containing 50 mL of a mixed aqueous solution of formic acid...
PUM
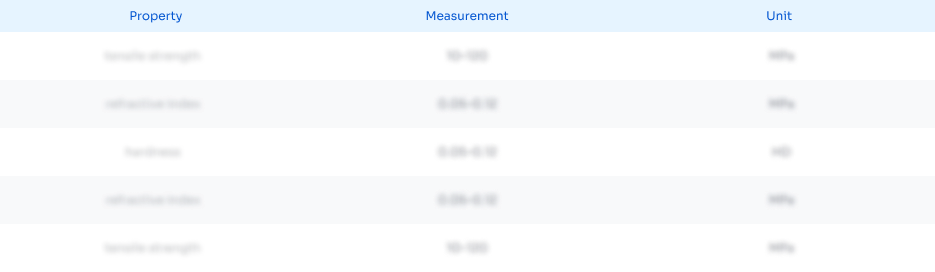
Abstract
Description
Claims
Application Information

- R&D
- Intellectual Property
- Life Sciences
- Materials
- Tech Scout
- Unparalleled Data Quality
- Higher Quality Content
- 60% Fewer Hallucinations
Browse by: Latest US Patents, China's latest patents, Technical Efficacy Thesaurus, Application Domain, Technology Topic, Popular Technical Reports.
© 2025 PatSnap. All rights reserved.Legal|Privacy policy|Modern Slavery Act Transparency Statement|Sitemap|About US| Contact US: help@patsnap.com