Detection robot based on negative pressure adsorption
A robot and negative pressure technology, applied in motor vehicles, optical testing flaws/defects, transportation and packaging, etc., can solve problems such as manual safety hazards, low work efficiency, and heavy inspection workload, so as to reduce inspection costs and improve work Efficiency and the effect of eliminating potential safety hazards
- Summary
- Abstract
- Description
- Claims
- Application Information
AI Technical Summary
Problems solved by technology
Method used
Image
Examples
Embodiment Construction
[0022] The present invention will be further described below in conjunction with the accompanying drawings.
[0023] Such as figure 1 As shown, a detection robot based on negative pressure adsorption of the present invention, the robot system includes a robot shell 1, a propulsion system 2, a left adjustment system 3, a positive pressure system 4, a detection system 5, an adsorption suction cup 6, and a right adjustment system 7. The control system 11, the robot shell 1 is provided with a positive pressure system 4, and the positive pressure system 4 will pass the robot positive pressure centrifugal fan 8 to make the detection robot close to the bottom of the bridge; the left and right sides of the robot shell 1 are respectively set There are left adjustment system 3 and right adjustment system 7, left adjustment system 3 and right adjustment system 7, when the robot needs to turn, adjust the speed of left centrifugal fan 12 and right centrifugal fan 13 to detect the left and ...
PUM
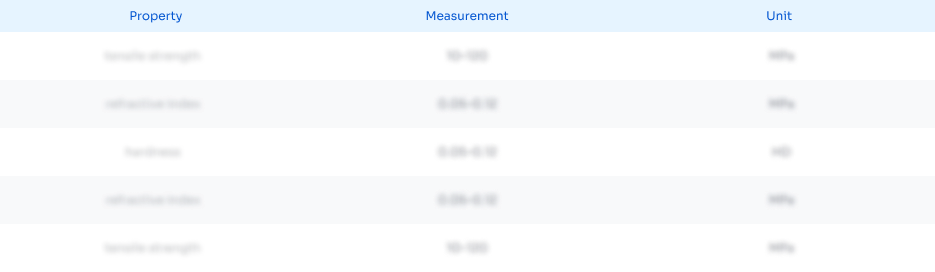
Abstract
Description
Claims
Application Information

- R&D
- Intellectual Property
- Life Sciences
- Materials
- Tech Scout
- Unparalleled Data Quality
- Higher Quality Content
- 60% Fewer Hallucinations
Browse by: Latest US Patents, China's latest patents, Technical Efficacy Thesaurus, Application Domain, Technology Topic, Popular Technical Reports.
© 2025 PatSnap. All rights reserved.Legal|Privacy policy|Modern Slavery Act Transparency Statement|Sitemap|About US| Contact US: help@patsnap.com