Coating method of RTV coating of supporting column insulator
A post insulator and coating method technology, applied in the direction of insulators, electrical components, circuits, etc., can solve the problems of paint dripping, long interval time, low production efficiency, etc., and achieve the effect of low environmental protection and safety pressure, and small health impact
- Summary
- Abstract
- Description
- Claims
- Application Information
AI Technical Summary
Problems solved by technology
Method used
Examples
Embodiment 1
[0037] A kind of coating method of pillar insulator RTV paint has the following steps:
[0038] (1) Clean the post insulators and pre-treat the metal fittings;
[0039] (2) Inspection and installation: connect the post insulator to the head of the equipment, and put the paint into the container; (inspection
[0040] Whether the post insulator has a certificate of conformity, whether the surface of the insulator has defects, cracks, damage, pores, mechanical impurities, oil stains that are difficult to clean), and the viscosity of the paint is 4# cup for 15 minutes.
[0041] (3) Coating: dip the post insulator in the paint for spin coating; the spin coating steps are dipping,
[0042] In the steps of material rejection and edge trimming, the solid content of the paint is 60%;
[0043] The impregnating step is to install the connection post insulator on the head of the coating equipment and place it in the horizontal direction.
[0044] Dip the insulator into the co...
Embodiment 2
[0055] Other steps are as in Example 1. The viscosity of the coating is to coat the 4# cup for 12 minutes, and the solid content of the coating is 55%. The dipping step is to install the connecting post insulator on the head of the coating equipment, place it in the horizontal direction, and then immerse in the coating and spin coating. Rotation speed 20r / min, time 2min.
[0056] The material throwing step is to make the insulator completely leave the coating liquid surface and then rotate for 5min at a speed of 50r / min.
[0057] The edge finishing step is to place the insulator in the horizontal direction while rotating, the surface dry time is 80min, and the speed is 5r / min.
[0058] The curing time is 48 hours, the temperature is 23°C, and the humidity is 65%;
Embodiment 3
[0060] Other steps are as in Example 1. The viscosity of the coating is to coat the 4# cup for 18 minutes, and the solid content of the coating is 65%. The dipping step is to install the connecting post insulator on the head of the coating equipment, place it in the horizontal direction, and then immerse in the coating to rotate the coating. The speed is 10r / min, and the time is 2.5min; the step of throwing the material is to make the insulator completely leave the coating liquid surface and then rotate for 3min, and the speed is 60r / min.
[0061] The edge finishing step is to place the insulator in the horizontal direction while rotating, the time is 60min, and the speed is 8r / min.
[0062] Standing curing time 72hr, temperature 20℃, humidity 60%;
PUM
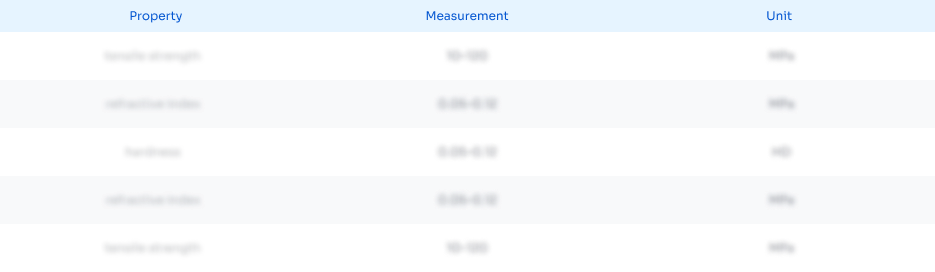
Abstract
Description
Claims
Application Information

- Generate Ideas
- Intellectual Property
- Life Sciences
- Materials
- Tech Scout
- Unparalleled Data Quality
- Higher Quality Content
- 60% Fewer Hallucinations
Browse by: Latest US Patents, China's latest patents, Technical Efficacy Thesaurus, Application Domain, Technology Topic, Popular Technical Reports.
© 2025 PatSnap. All rights reserved.Legal|Privacy policy|Modern Slavery Act Transparency Statement|Sitemap|About US| Contact US: help@patsnap.com