Ammonium paratungstate and preparation method thereof
A technology of ammonium paratungstate and ammonium tungstate, applied in the field of ammonium paratungstate and its preparation, can solve the problems of low metal recovery rate, difficulty in finding insoluble compounds for leaching and separation, uncontrollable product quality, etc., and achieve the effect of short process flow
- Summary
- Abstract
- Description
- Claims
- Application Information
AI Technical Summary
Problems solved by technology
Method used
Image
Examples
Embodiment 1
[0050] Using scheelite concentrate as raw material, the steps to prepare ammonium paratungstate are as follows:
[0051] (1) Take 100g of scheelite concentrate that has been ground, add 2 times the theoretical amount of ammonium phosphate, and mix;
[0052] (2) The mixed scheelite concentrate and ammonium phosphate were roasted for 1 hour at a reaction temperature of 830° C. to obtain a fired product, which was detected to be tungsten trioxide and calcium pyrophosphate;
[0053] (3) crushing the burnt product;
[0054] (4) dissolving the crushed product in ammonia water in a high-pressure decomposition kettle to obtain a crude ammonium tungstate solution, and the decomposition rate of tungsten trioxide reaches 98.9%;
[0055] (5) The crude ammonium tungstate solution is removed through processes such as sulfidation-precipitation to obtain pure ammonium tungstate solution;
[0056] (6) Evaporate and crystallize the pure ammonium tungstate solution after impurity removal to ob...
Embodiment 2
[0058] Using scheelite concentrate as raw material, the steps to prepare ammonium paratungstate are as follows:
[0059] (1) Take 100g of scheelite concentrate that has been ground, add 2.5 times the theoretical amount of red phosphorus, and mix;
[0060] (2) The mixed scheelite concentrate and ammonium phosphate were roasted for 1 hour at a reaction temperature of 800° C. to obtain a fired product, which was detected as tungsten trioxide and calcium pyrophosphate;
[0061] (3) Crushing the burnt material;
[0062] (4) dissolving the crushed product in ammonia water in a high-pressure decomposition kettle to obtain a crude ammonium tungstate solution, and the decomposition rate of tungsten trioxide reaches 98.6%;
[0063] (5) The crude ammonium tungstate solution is removed through processes such as sulfidation-precipitation to obtain pure ammonium tungstate solution;
[0064] (6) Evaporate and crystallize the pure ammonium tungstate solution after impurity removal to obtain...
Embodiment 3
[0066] Using scheelite concentrate as raw material, the steps to prepare ammonium paratungstate are as follows:
[0067] (1) Take 100g of scheelite concentrate that has been ground, add 2 times the theoretical amount of ammonium phosphate, and mix;
[0068] (2) The mixed scheelite concentrate and ammonium phosphate were roasted for 1 hour at a reaction temperature of 800° C. to obtain a fired product, which was detected to be tungsten trioxide and calcium pyrophosphate;
[0069] (3) crushing the burnt product;
[0070] (4) dissolving the broken product in ammonia water in a high-pressure decomposition kettle to obtain a crude ammonium tungstate solution, and the decomposition rate of tungsten trioxide reaches 99.1%;
[0071] (5) The crude ammonium tungstate solution is removed through processes such as sulfidation-precipitation to obtain pure ammonium tungstate solution;
[0072] (6) Evaporate and crystallize the pure ammonium tungstate solution after impurity removal to obt...
PUM
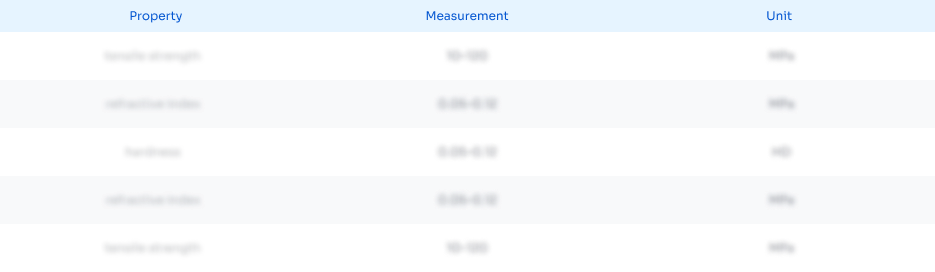
Abstract
Description
Claims
Application Information

- Generate Ideas
- Intellectual Property
- Life Sciences
- Materials
- Tech Scout
- Unparalleled Data Quality
- Higher Quality Content
- 60% Fewer Hallucinations
Browse by: Latest US Patents, China's latest patents, Technical Efficacy Thesaurus, Application Domain, Technology Topic, Popular Technical Reports.
© 2025 PatSnap. All rights reserved.Legal|Privacy policy|Modern Slavery Act Transparency Statement|Sitemap|About US| Contact US: help@patsnap.com