Method for using hydrogen and carbon monoxide to separate cold box tail gas as reformer fuel
A carbon monoxide and reformer technology, applied in chemical instruments and methods, hydrogen, inorganic chemistry, etc., can solve the problems of tail gas waste and lack of reuse of tail gas economic value, and achieve the effects of reducing CO2 emissions, saving fuel, and pipeline safety
- Summary
- Abstract
- Description
- Claims
- Application Information
AI Technical Summary
Problems solved by technology
Method used
Image
Examples
Embodiment 1
[0025] A method of using hydrogen and carbon monoxide to separate cold box tail gas as reformer fuel, the process flow is as follows figure 1 As shown, a part of the tail gas in the cold box 1 is connected to the torch 2 for combustion through the discharge pipe 4, and the remaining cold box tail gas is connected to the reformer 3 through the tail gas reuse pipe 6 as the reformer fuel; The first regulating valve 5 for the flow and pressure of the cold box tail gas of combustion is provided. The tail gas reuse pipeline 6 is provided with a second regulating valve 7 for adjusting the flow and pressure of the cold box tail gas entering the reformer combustion. The tail gas reuse pipe 6 is also provided with There is a hand valve to control the opening and closing of the pipeline. The reformer 3 is a reformer for steam methane reforming (SMR).
[0026] The method specifically includes the following steps:
[0027] (1) Open the reformer to make it run normally;
[0028] (2) adju...
Embodiment 2
[0033] A method of how to lead the cold box tail gas to the SMR reformer:
[0034] (1) The SMR reformer has been started and is in normal production;
[0035] (2) Process setting, open all hand valves on the reutilization pipeline from the cold box exhaust gas to the SMR reformer exhaust gas.
[0036] (3) Regulate the regulating valve on the discharge pipeline so that the pressure of the cold box tail gas entering the torch combustion is adjusted to 0.6 bar;
[0037] (4) Regulate the regulating valve on the tail gas reuse pipeline, so that the pressure of the cold box tail gas entering the reformer combustion is adjusted to 0.7 bar;
[0038] (5) Control the flow rate of the cold box exhaust gas entering the reformer to be 0m 3 / h.
[0039] (6) The valve opening degree of the second regulating valve is 0%, and the first regulating valve is opened, and now the tail gas is all vented and burned.
Embodiment 3
[0041] A method of how to lead the cold box tail gas to the SMR reformer:
[0042] (1) The SMR reformer has been started and is in normal production;
[0043] (2) Process setting, open all hand valves on the reutilization pipeline from the cold box exhaust gas to the SMR reformer exhaust gas.
[0044] (3) adjust the regulating valve on the discharge pipeline so that the pressure of the cold box tail gas entering the torch combustion is adjusted to 0.8 bar;
[0045] (4) Regulate the regulating valve on the tail gas reuse pipeline, so that the pressure of the cold box tail gas entering the reformer combustion is adjusted to 0.4 bar;
[0046] (5) Control the flow rate of the cold box exhaust gas entering the reformer to be 100m 3 / h.
[0047] (6) The opening degree of the first regulating valve is 0%, and the second regulating valve is opened. At this time, all the tail gas is led to the SMR reformer for combustion.
PUM
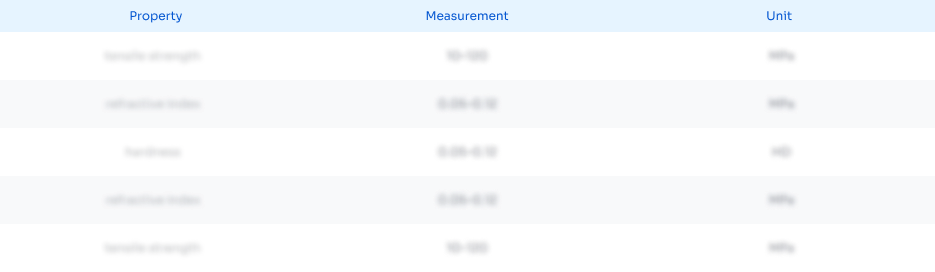
Abstract
Description
Claims
Application Information

- R&D
- Intellectual Property
- Life Sciences
- Materials
- Tech Scout
- Unparalleled Data Quality
- Higher Quality Content
- 60% Fewer Hallucinations
Browse by: Latest US Patents, China's latest patents, Technical Efficacy Thesaurus, Application Domain, Technology Topic, Popular Technical Reports.
© 2025 PatSnap. All rights reserved.Legal|Privacy policy|Modern Slavery Act Transparency Statement|Sitemap|About US| Contact US: help@patsnap.com