Anti-staining dyeing method of polyamide-cotton fabric
A dyeing method and anti-staining technology, which is applied in the field of anti-staining of nylon and cotton dyed with reactive dyes, can solve the problems of reducing the color fixation rate, increasing the color and luster of dyeing wastewater and the amount of COD, and affecting the utilization rate of dyes, etc., so as to improve coloring High efficiency, good nylon jacquard whiteness, anti-staining and leveling effect, reducing COD amount and color depth
- Summary
- Abstract
- Description
- Claims
- Application Information
AI Technical Summary
Problems solved by technology
Method used
Image
Examples
Embodiment 1
[0040] Conventional dyeing method: Dye the gray cloth at a temperature of 40°C, and add reactive black 5# dye (dyeing depth: 2.0%) and sodium sulfate (the concentration of sodium sulfate in the dyeing system is 60g / L) in the water bath in sequence. , then heat up to 60°C at a rate of 1°C / min and keep the color for 30 minutes, then add soda ash (the concentration of soda ash in the dyeing system is 20g / L) and keep it for 60 minutes, and finally cool down to 45°C for post-treatment.
[0041] The post-treatment process is as follows: After removing the dyeing residue, wash once with warm water at 40-45°C, then soap with hot water at 95-98°C, and finally wash once with cold water to complete the entire dyeing process.
Embodiment 2
[0043]Dye the gray cloth at a temperature of 40°C, add reactive black 5# dye (the dyeing depth is 2.0%) and sodium sulfate (the concentration of sodium sulfate in the dyeing system is 60g / L) in a water bath to absorb color for 10 minutes , add soda ash (the concentration of soda ash in the dyeing system is 0.05g / L) and keep warm for 30 minutes, then add soda ash (the concentration of soda ash in the dyeing system is 15g / L) and heat up to 50°C at a rate of 1°C / min. After dyeing for 30 minutes, continue to heat up to 70°C at a heating rate of 2°C / min, then keep warm for 15 minutes to complete the dyeing, and then cool down to 45°C for post-treatment.
[0044] The post-treatment process is as follows: After removing the dyeing residue, first wash with warm water at 40-45°C, then add cold water to heat up to 80°C for one wash, then add hot water at 90-95°C for soaping, and finally wash with warm water at 50-55°C Wash once, and remove the residual liquid after each washing to preve...
Embodiment 3
[0046] Dye the gray cloth at a temperature of 40°C, add reactive black 5# dye (the dyeing depth is 2.0%) and sodium sulfate (the concentration of sodium sulfate in the dyeing system is 60g / L) in a water bath, and then add soda ash (The concentration of soda ash in the dyeing system is 15g / L). Raise the temperature at a rate of 1°C / min to 50°C and keep the color for 30 minutes, then continue to heat up to 70°C and keep the temperature for 15 minutes at a rate of 2°C / min. Post-treatment after 45°C.
[0047] The post-treatment process is as follows: After removing the dyeing residue, first wash with warm water at 40-45°C, then add cold water to heat up to 80°C for one wash, then add hot water at 90-95°C for soaping, and finally wash with warm water at 50-55°C Wash once, and remove the residual liquid after each washing to prevent the residual liquid from contaminating again.
PUM
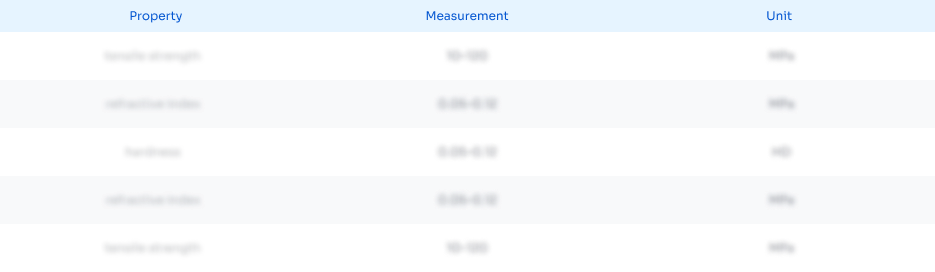
Abstract
Description
Claims
Application Information

- R&D
- Intellectual Property
- Life Sciences
- Materials
- Tech Scout
- Unparalleled Data Quality
- Higher Quality Content
- 60% Fewer Hallucinations
Browse by: Latest US Patents, China's latest patents, Technical Efficacy Thesaurus, Application Domain, Technology Topic, Popular Technical Reports.
© 2025 PatSnap. All rights reserved.Legal|Privacy policy|Modern Slavery Act Transparency Statement|Sitemap|About US| Contact US: help@patsnap.com