Method for manufacturing semiconductor chips and surface protective tape for thin-film grinding used in same
A manufacturing method and semiconductor technology, which can be used in the manufacture of semiconductor/solid-state devices, semiconductor devices, film/sheet adhesives, etc. The effect of precision and simple manufacturing methods
- Summary
- Abstract
- Description
- Claims
- Application Information
AI Technical Summary
Problems solved by technology
Method used
Image
Examples
Embodiment 1
[0251] (I) Fabrication of Surface Protection Tape for Thin Film Polishing
[0252] An ultraviolet curable (meth)acrylic adhesive layer is provided on a substrate film made of ethylene-acrylic acid copolymer with a thickness of 100 μm, and a (meth)acrylic copolymer containing epoxy resin is placed on the adhesive layer. An adhesive layer composed of a substance was used to produce the surface protection tape for film polishing of the present invention.
[0253] (1) Manufacturing method of adhesive tape
[0254] Blend 78 mol% of 2-ethylhexyl acrylate, 21 mol% of 2-hydroxyethyl acrylate, and 1 mol% of methacrylic acid, and copolymerize them in an ethyl acetate solution to obtain a copolymer solution with a weight average molecular weight of 700,000 . With respect to 100 parts by mass of the copolymer, 5.0 parts by mass of 2-methacryloyloxyethyl isocyanate (trade name, Karenz MOI manufactured by Showa Denko Co., Ltd.) was mixed in the solution, and they were mixed in the solutio...
Embodiment 2
[0276] Using the surface protection tape for film polishing made in Example 1, the process of (6) in Example 1 is changed to the process of the following (6-1) to (6-2), and in addition, A semiconductor chip was produced in the same manner as in Example 1.
[0277] (6-1) The pick-up tape (11) was expanded under conditions of a speed of 1 mm / sec and an expansion amount of 8 mm so as to divide only the semiconductor wafer.
[0278] (6-2) After the above expansion, the adhesive film (adhesive layer) (6) is cut with a laser ( 14 ). { figure 2 Process shown in (7-1B)}
Embodiment 3
[0280] by figure 1 and image 3 The process of making semiconductor chips.
[0281] Use the surface protection tape for film polishing that is made in embodiment 1, after carrying out the process of (1)~(3) in embodiment 1, carry out following process (4A)~(6A) instead of (4)~( 7), Manufacturing semiconductor chips.
[0282] (4A) Attach the same expansion tape (11) (fixation tape (21)) as in Example 1 to the base film (4) side of the film polishing surface protection tape, and fix it to the ring frame (22) . The expanding tape (11) (fixing tape (21)) has an adhesive layer made of an ultraviolet-curable acrylic copolymer on a base film made of vinyl ionomer resin.
[0283] (5A) Expand the above-mentioned fixing tape (21) at a speed of 1 mm / sec and an expansion amount of 20 mm, and divide the adhesive film (adhesive layer) (6) from the semiconductor wafer on the adhesive film (3). .
[0284] (6A) The divided semiconductor wafer (10A) becomes each chip (27) with an adhesive...
PUM
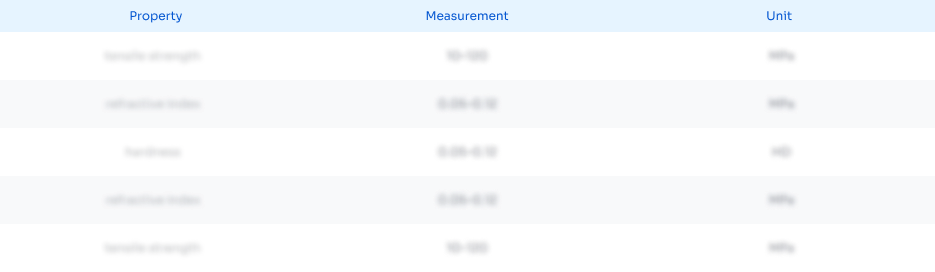
Abstract
Description
Claims
Application Information

- R&D
- Intellectual Property
- Life Sciences
- Materials
- Tech Scout
- Unparalleled Data Quality
- Higher Quality Content
- 60% Fewer Hallucinations
Browse by: Latest US Patents, China's latest patents, Technical Efficacy Thesaurus, Application Domain, Technology Topic, Popular Technical Reports.
© 2025 PatSnap. All rights reserved.Legal|Privacy policy|Modern Slavery Act Transparency Statement|Sitemap|About US| Contact US: help@patsnap.com