Multi-manifold valve seat
A valve seat and valve installation technology, which is used in multi-port valves, valve devices, fluid pressure actuation devices, etc., can solve the problems of difficult quality control, easy fluctuations in processing quality, and large installation space occupied by the pilot valve seat. Achieve the effect of solving the limited number of CNC tool positions, solving the high requirements for product sealing, and reducing the difficulty of processing technology
- Summary
- Abstract
- Description
- Claims
- Application Information
AI Technical Summary
Problems solved by technology
Method used
Image
Examples
Embodiment Construction
[0020] In order to better understand the present invention, the implementation manner of the present invention will be explained in detail below in conjunction with the accompanying drawings.
[0021] Such as Figure 1 to Figure 6 As shown, a multi-unit valve seat includes a valve seat body 1. The valve seat body 1 is provided with a plurality of air grooves 1 31 and 2 32 on the end face 2 connected to the valve cover. 31. The bottom of the air tank 2 32 is respectively provided with a valve nozzle installation hole 1 41 and a valve nozzle installation hole 2 42 which are vertically arranged. Mouth one 16, valve mouth two 15, be provided with the air inlet channel one 5 that is connected with air groove one 31 at valve mouth mounting hole 41 one sides, air inlet channel one 5 is connected with input port one 13, input port one 13 is located at The right end face 12 bottom of valve seat body, the right end face 12 upper part of valve seat body is provided with air inlet passag...
PUM
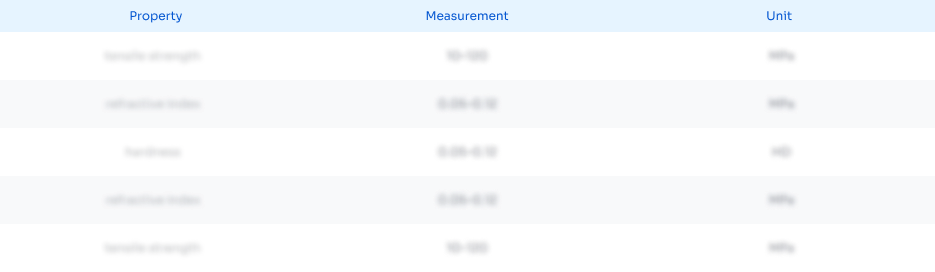
Abstract
Description
Claims
Application Information

- R&D
- Intellectual Property
- Life Sciences
- Materials
- Tech Scout
- Unparalleled Data Quality
- Higher Quality Content
- 60% Fewer Hallucinations
Browse by: Latest US Patents, China's latest patents, Technical Efficacy Thesaurus, Application Domain, Technology Topic, Popular Technical Reports.
© 2025 PatSnap. All rights reserved.Legal|Privacy policy|Modern Slavery Act Transparency Statement|Sitemap|About US| Contact US: help@patsnap.com