Aqueous polyurethane waterproof paint and preparation method thereof
A technology of water-based polyurethane and waterproof coatings, which is applied in the preparation of coatings and in the field of water-based polyurethane waterproof coatings. It can solve the problems of lack of mature technology and achieve the effects of strong self-cleaning, easy-to-obtain raw materials and high bonding strength.
- Summary
- Abstract
- Description
- Claims
- Application Information
AI Technical Summary
Problems solved by technology
Method used
Examples
Embodiment l
[0044] Add 1 part of N-methylol acrylamide and 0.5 parts of citric acid in sequence in the reaction kettle, wherein, N-methylol acrylamide needs to be diluted, that is, add 2 kg of N-methylol acrylamide by weight Dissolve ethanol with a concentration of 50-70%, then stir and raise the temperature. Before the temperature rises to 62°C, add 40 parts of polyurethane prepolymer at one time, then raise the temperature to 82°C, keep the reaction at 83°C for 2 hours, and cool down to Discharge at 52°C to obtain component A; mix 16 parts of inorganic fillers in component B (10 parts of schist-type high-quality sericite powder, the diameter-thickness ratio of the wafer is 50-60 times, and the original average particle size of 6 parts d=1~ 5 μm micronized calcium carbonate), 2 parts of dibutyl phthalate, 1 part of crosslinking agent (0.5 part of monoalkoxypyrophosphate titanate coupling agent, 0.5 part of isopropanol), 0.1 part of Disc-40, 0.1 part of tributyl phosphate, 0.5 part of tri...
Embodiment 2
[0046] Add 1.5 parts of N-methylolacrylamide and 0.7 parts of citric acid in sequence in the reaction kettle. Among them, N-methylolacrylamide needs to be diluted, that is, add 2 kg of N-methylolacrylamide by weight Dissolve ethanol with a concentration of 50-70%, then stir and raise the temperature. Before the temperature rises to 62°C, add 45 parts of polyurethane prepolymer at one time, then raise the temperature to 82°C, keep the reaction at 84°C for 2.5 hours, and cool down to Discharge at 53°C to get component A; mix 18 parts of inorganic fillers in component B (11 parts of schist-type high-quality sericite powder, the diameter-thickness ratio of the wafer is 50-60 times, and 7 parts of the original average particle size d=1~ 5μm micronized calcium carbonate), 3 parts of dibutyl phthalate, 2 parts of crosslinking agent (1 part of monoalkoxypyrophosphate titanate coupling agent, 1 part of isopropanol), 0.2 parts of Si Disc-60, 0.2 part of tributyl phosphate, 0.7 part of t...
Embodiment 3
[0048] Add 2 parts of N-methylolacrylamide and 1 part of citric acid in sequence in the reaction kettle. Among them, N-methylolacrylamide needs to be diluted, that is, add 2 kg of N-methylolacrylamide by weight Dissolve ethanol with a concentration of 50-70%, then stir and raise the temperature. Before the temperature rises to 62°C, add 50 parts of polyurethane prepolymer at one time, then raise the temperature to 82°C, keep the reaction at 85°C for 2.5 hours, and cool down to Discharge at 54°C to obtain component A; mix 24 parts of inorganic fillers in component B (15 parts of schist-type high-quality sericite powder, the diameter-thickness ratio of the wafer is 50-60 times, and 9 parts of the original average particle size d=1~ 5μm micronized calcium carbonate), 5 parts of dibutyl phthalate, 3 parts of crosslinking agent (1.5 parts of monoalkoxypyrophosphate titanate coupling agent, 1.5 parts of isopropanol), 0.3 parts of Si Pan-80, 0.3 part of tributyl phosphate, 1 part of ...
PUM
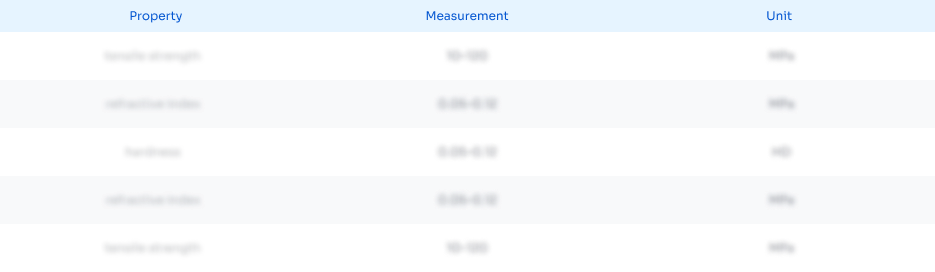
Abstract
Description
Claims
Application Information

- Generate Ideas
- Intellectual Property
- Life Sciences
- Materials
- Tech Scout
- Unparalleled Data Quality
- Higher Quality Content
- 60% Fewer Hallucinations
Browse by: Latest US Patents, China's latest patents, Technical Efficacy Thesaurus, Application Domain, Technology Topic, Popular Technical Reports.
© 2025 PatSnap. All rights reserved.Legal|Privacy policy|Modern Slavery Act Transparency Statement|Sitemap|About US| Contact US: help@patsnap.com