A carbonaceous conductive slag for electroslag steel smelting
A conductive slag and electroslag technology, applied in the field of electroslag steel smelting, can solve the problems of high Ti content at the bottom of electroslag ingots, unsuitable for smelting low-titanium steel grades, and scrapping, etc., and achieves high production efficiency and convenient arcing slag , the effect of low cost
- Summary
- Abstract
- Description
- Claims
- Application Information
AI Technical Summary
Problems solved by technology
Method used
Image
Examples
Embodiment 1
[0013] Embodiment 1: according to the ratio in parts by weight: carbon powder: fluorite powder: Na 2 SiO 3 Aqueous solution = 72:24:4 ratio Weigh raw materials, first mix carbon powder, fluorite powder, and then Na 2 SiO 3 The aqueous solution is added to the mixture of carbon powder and fluorite powder, stirred, mixed evenly, made into small pieces using a molding die, and dried for later use; wherein Na 2 SiO 3 The concentration of the aqueous solution is 20%.
Embodiment 2
[0014] Embodiment 2: according to the ratio of parts by weight: carbon powder: fluorite powder: Na 2 SiO 3 Aqueous solution = 75:21:4 ratio to weigh raw materials, first mix carbon powder and fluorite powder evenly, and then Na 2 SiO 3 The aqueous solution is added to the mixture of carbon powder and fluorite powder, stirred, mixed evenly, made into small pieces using a molding die, and dried for later use; wherein Na 2 SiO 3 The concentration of the aqueous solution is 24%.
Embodiment 3
[0015] Embodiment 3: according to the ratio in parts by weight: carbon powder: fluorite powder: Na 2 SiO 3 Aqueous solution = 73:22:5 ratio to weigh raw materials, first mix carbon powder and fluorite powder evenly, and then Na 2 SiO 3 The aqueous solution is added to the mixture of carbon powder and fluorite powder, stirred, mixed evenly, made into small pieces using a molding die, and dried for later use; wherein Na 2 SiO 3 The concentration of the aqueous solution is 26%.
[0016] The carbonaceous conductive slag prepared according to the above examples 1-3 is respectively called carbonaceous conductive slag 1, carbonaceous conductive slag 2, and carbonaceous conductive slag 3. Use electric welding machine welding clips to test its conductivity and arcing stability, and the results As shown in Table 1.
[0017] Table 1 uses Na 2 SiO 3 Carbonaceous conductive slag in aqueous solution and Na-free 2 SiO 3 Performance comparison of carbonaceous conductive slag in aqueo...
PUM
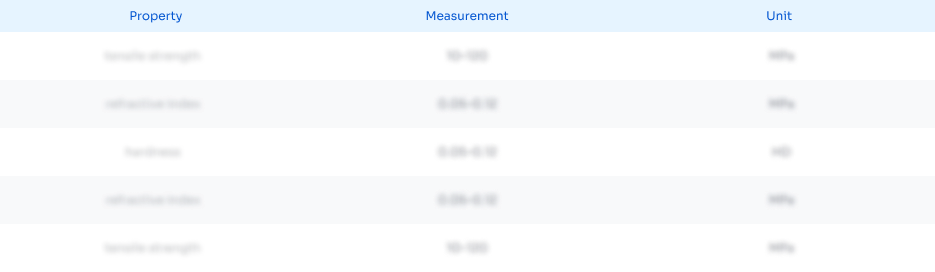
Abstract
Description
Claims
Application Information

- Generate Ideas
- Intellectual Property
- Life Sciences
- Materials
- Tech Scout
- Unparalleled Data Quality
- Higher Quality Content
- 60% Fewer Hallucinations
Browse by: Latest US Patents, China's latest patents, Technical Efficacy Thesaurus, Application Domain, Technology Topic, Popular Technical Reports.
© 2025 PatSnap. All rights reserved.Legal|Privacy policy|Modern Slavery Act Transparency Statement|Sitemap|About US| Contact US: help@patsnap.com