Curved surface workpiece surface array microstructure graph layout method
A technology for surface workpiece and graphic layout, applied in manufacturing tools, metal processing equipment, welding equipment, etc., can solve the problems of micro-structure graphic layout and processing deviation, tool orientation error projection splicing error, not considering errors, etc., to eliminate the layout. The effects of machining errors, easy adjustment, and neat spatial orientation
- Summary
- Abstract
- Description
- Claims
- Application Information
AI Technical Summary
Problems solved by technology
Method used
Examples
Embodiment Construction
[0023] The present invention will be described in further detail below in combination with specific embodiments.
[0024] The invention provides a surface array microstructure graphic layout method of a curved surface workpiece. By adopting the method, a periodic array microstructure can be arranged and prepared on a given free-form surface workpiece surface with a smooth surface, and then the array microstructure can be laid out. Processing; wherein, the periodic unit spacing between the unit microstructures that constitute the periodic array microstructure is D; the definition of the periodic unit spacing is the arc length along the curved surface between the respective geometric center points of any two unit microstructures or Space straight-line distance (choose one of the two, once determined, it will be consistent throughout the method). If the periodic unit spacing defines the arc length along the curved surface, then the "distance" mentioned in the present invention al...
PUM
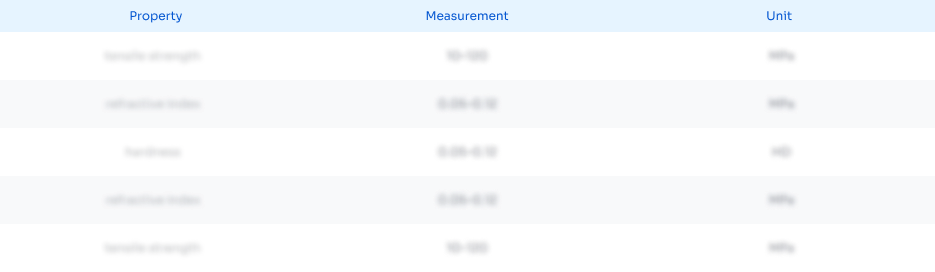
Abstract
Description
Claims
Application Information

- R&D
- Intellectual Property
- Life Sciences
- Materials
- Tech Scout
- Unparalleled Data Quality
- Higher Quality Content
- 60% Fewer Hallucinations
Browse by: Latest US Patents, China's latest patents, Technical Efficacy Thesaurus, Application Domain, Technology Topic, Popular Technical Reports.
© 2025 PatSnap. All rights reserved.Legal|Privacy policy|Modern Slavery Act Transparency Statement|Sitemap|About US| Contact US: help@patsnap.com