Heat treatment carburization process of carburizing steel
A carburizing steel and carburizing technology, which is applied in the field of heat treatment of metal materials, can solve problems such as the inability to meet requirements in service performance, and achieve the effects of avoiding carbide coarsening, increasing carbon content, and improving wear resistance.
- Summary
- Abstract
- Description
- Claims
- Application Information
AI Technical Summary
Problems solved by technology
Method used
Image
Examples
Embodiment 1
[0025] according to image 3 The process curve diagram is carried out:
[0026] (1) Pre-carburization: Pre-carburize for 1h at 830°C and carbon potential of 1.1;
[0027] (2) Cyclic carburizing: Carburizing at 920°C, carbon potential 1.1 for 3 hours, and then cooling in oil at 100°C; after that, carburizing at 920°C, carbon potential 1.1 for 3 hours, and then at 100°C The process step of cooling in oil is cycled once, thereby completing the cyclic carburization with 2 cycles;
[0028] (3) Diffusion and quenching: use 920 °C, carbon potential 1.0, and carry out carburizing diffusion for 2 hours to obtain a gentle carbon concentration distribution and reduce the stress caused by carburizing heat treatment; after diffusion, cool the temperature to 860 °C, carbon potential 1.0, after holding for 1h, quench and cool in oil at 100℃;
[0029] (4) Tempering: Tempering at 180°C for 3h.
[0030] After completion, use the peeling method to detect the surface carbide content: the carb...
Embodiment 2
[0032] according to Figure 4 The process curve diagram is carried out:
[0033] (1) Pre-carburization: pre-carburize for 2 hours at 800°C and carbon potential of 0.9;
[0034] (2) Cyclic carburizing: Carburizing at 910°C and carbon potential of 0.9 for 1 hour, and then cooling in oil at 50°C; after that, carburizing at 910°C and carbon potential of 0.9 for 1 hour, and then at 50°C for 1 hour. The process step of cooling in oil is cycled once, thereby completing the cyclic carburization with 2 cycles;
[0035] (3) Diffusion and quenching: use 910 °C, carbon potential 1.0, and carry out carburizing diffusion for 2 hours to obtain a gentle carbon concentration distribution and reduce the stress caused by carburizing heat treatment; after diffusion, cool the temperature to 860 °C, carbon potential 1.0, after holding for 1h, quench and cool in oil at 100℃;
[0036] (4) Tempering: Tempering at 180°C for 3h.
[0037] After completion, use the peeling method to detect the surface...
Embodiment 3
[0039] according to Figure 5 The process curve diagram is carried out:
[0040] (1) Pre-carburization: pre-carburize for 3 hours at 840°C with a carbon potential of 1.3;
[0041] (2) Cyclic carburizing: Carburizing at 940°C, carbon potential 1.3 for 4 hours, and then cooling in oil at 130°C; after that, carburizing at 940°C, carbon potential 1.3 for 4 hours, and then at 130°C The process step of cooling in oil is cycled once, thereby completing the cyclic carburization with 2 cycles;
[0042] (3) Diffusion and quenching: use 940°C, carbon potential 1.0, and carry out 2h carburizing diffusion to obtain a gentle carbon concentration distribution and reduce the stress caused by carburizing heat treatment; after diffusion, cool the temperature to 900°C, carbon potential 0.8, after holding for 1h, quench and cool in oil at 100℃;
[0043] (4) Tempering: Tempering at 180°C for 3h.
[0044] After completion, use the peeling method to detect the surface carbide content: the carbid...
PUM
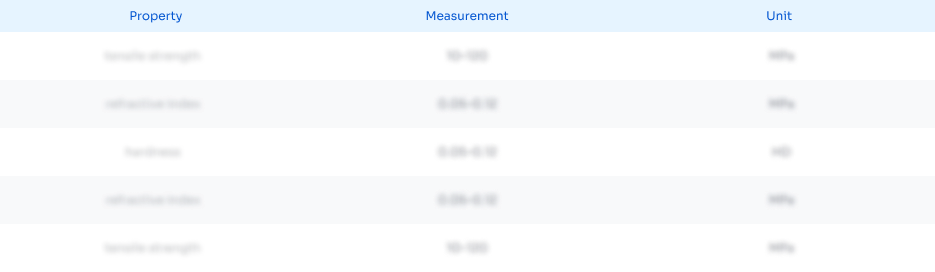
Abstract
Description
Claims
Application Information

- R&D
- Intellectual Property
- Life Sciences
- Materials
- Tech Scout
- Unparalleled Data Quality
- Higher Quality Content
- 60% Fewer Hallucinations
Browse by: Latest US Patents, China's latest patents, Technical Efficacy Thesaurus, Application Domain, Technology Topic, Popular Technical Reports.
© 2025 PatSnap. All rights reserved.Legal|Privacy policy|Modern Slavery Act Transparency Statement|Sitemap|About US| Contact US: help@patsnap.com