Petroleum coke material calcination cooling device
A cooling device and petroleum coke technology, applied in the field of oil slurry equipment, can solve the problems of large heat loss, low heat recovery efficiency and high operating cost, and achieve the effects of energy saving, simple results and safe use.
- Summary
- Abstract
- Description
- Claims
- Application Information
AI Technical Summary
Problems solved by technology
Method used
Image
Examples
Embodiment 1
[0025] In this example, if figure 1 As shown, a petroleum coke calcination cooling device includes a cylinder 1-7 and a rim 1-13, and the cylinder 1-7 is respectively provided with a material inlet 1-1, a material outlet 1-8, and a rim 1-13, the material inlet 1-1 and the material outlet 1-8 are respectively located at the two ends of the cylinder body 1-7, and there is a rim 1-13 at the two ends of the material inlet 1-1 and the material outlet 1-8 respectively, and the The barrel 1-7 also includes a cooling body 1-5, which is connected to the material inlet 1-1, and the cooling body 1-5 is provided with an air inlet 1-2 and an air outlet 1-10, and the cooling body 1-5 is larger in diameter than cylinder 1-7. The rim 1-13 at both ends of the material inlet 1-1 and the material outlet 1-8 of the cooling device is fixedly connected to the support plane through the idler roller 1-9, and the cooling main body 1-5 is fixedly connected to the support plane through the support fram...
Embodiment 2
[0029] In this embodiment, the number of support frames 1-4 is 5, the wall thickness of the cooling main body 1-5 is 3.0 cm, and the thickness of the aluminized polyimide film and the airgel felt film is 0.5 mm. Other structures are the same as in Example 1, and the heat recovery efficiency of this example is increased to 31%.
Embodiment 3
[0031] In this embodiment, the number of support frames 1-4 is 5, the wall thickness of the cooling main body 1-5 is 1.5 cm, and the thickness of the aluminized polyimide film and the airgel felt film is 0.4 mm. Other structures are the same as in Example 1, and the heat recovery efficiency of this example is increased to 33%.
PUM
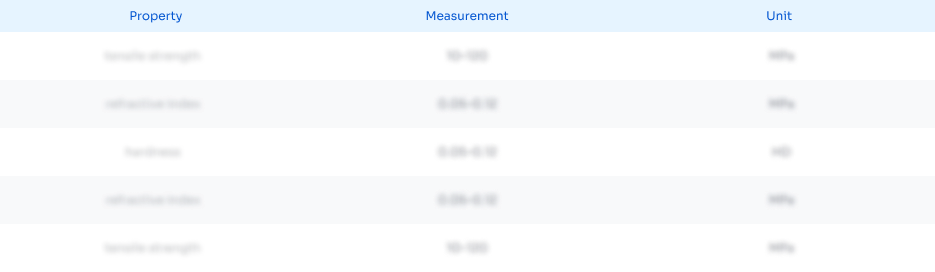
Abstract
Description
Claims
Application Information

- R&D Engineer
- R&D Manager
- IP Professional
- Industry Leading Data Capabilities
- Powerful AI technology
- Patent DNA Extraction
Browse by: Latest US Patents, China's latest patents, Technical Efficacy Thesaurus, Application Domain, Technology Topic, Popular Technical Reports.
© 2024 PatSnap. All rights reserved.Legal|Privacy policy|Modern Slavery Act Transparency Statement|Sitemap|About US| Contact US: help@patsnap.com