Hot working method capable of simultaneously improving electrical conductivity and strength of aluminum alloy
An aluminum alloy and electrical conductivity technology, which is applied in the field of thermal processing to simultaneously improve the electrical conductivity and strength of aluminum alloys, can solve the problems of unstable conductivity of rare earth aluminum conductors, low strength of aluminum alloys, complex rare earth components, etc. High conductivity, high strength effect
- Summary
- Abstract
- Description
- Claims
- Application Information
AI Technical Summary
Problems solved by technology
Method used
Image
Examples
specific Embodiment approach
[0039] The thermal processing preparation method of the present invention is further explained and illustrated with data in conjunction with examples below, but the present invention is not limited to these examples.
[0040] For the convenience of comparison, the aluminum alloy used in the examples is a 6××× series (Al—Mg—Si—Cu) aluminum alloy. The specific chemical composition of this alloy is: Mg 0.75wt.%, Si0.75wt.%, Cu 0.8wt.%, Mn 0.15wt.%, Cr 0.15wt.%, Ti 0.01wt.%, Fe 0.20wt. %, and the rest is aluminum. Comparative example also adopts above-mentioned aluminum alloy, and specific method adopts traditional preparation method, such as figure 2 shown. The hardness test is to use HXD-1000T Vickers hardness testing machine to test the hardness of samples with different aging processes. The applied load is 4.9N, and the loading time is 10s. At least 5 points are tested for each sample, and the maximum and minimum values are removed, and the remaining average is calculated...
Embodiment 1
[0044] 6××× aluminum alloy ingots were homogenized in a circulating air resistance furnace at 550°C for 24 hours, then cut and milled, hot rolled into 5mm thick plates, and then solidified in an air circulating resistance furnace at 560°C for 30 minutes. Solvent treatment and water quenching. Then the plate was treated in an oil bath furnace at 250° C. for 1 hour, and finally cold-rolled into a 4 mm thick thin plate (deformation amount 20%) through multiple passes. Subsequently, the plates were subjected to aging treatment at 180°C, 210°C, and 240°C for different times in an oil bath furnace, and the electrical conductivity and hardness of the samples were tested, and then tensile tests were carried out on typical aging aluminum alloys. The artificial aging was carried out in an oil bath furnace with a temperature control accuracy of ±2°C.
Embodiment 2
[0046] 6××× aluminum alloy ingots were homogenized in a circulating air resistance furnace at 550°C for 24 hours, then cut and milled, hot rolled into 5mm thick plates, and then solidified in an air circulating resistance furnace at 560°C for 30 minutes. Solvent treatment and water quenching. Then the plate was treated in an oil bath furnace at 250° C. for 1 hour, and finally cold-rolled into a 3 mm thick thin plate (40% deformation) through multiple passes. Subsequently, the plates were subjected to aging treatment at 180°C, 210°C, and 240°C for different times in an oil bath furnace, and the electrical conductivity and hardness of the samples were tested, and then tensile tests were carried out on typical aging aluminum alloys. The artificial aging was carried out in an oil bath furnace with a temperature control accuracy of ±2°C.
PUM
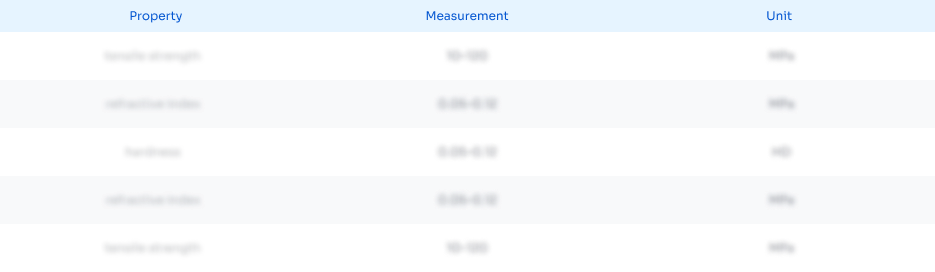
Abstract
Description
Claims
Application Information

- R&D
- Intellectual Property
- Life Sciences
- Materials
- Tech Scout
- Unparalleled Data Quality
- Higher Quality Content
- 60% Fewer Hallucinations
Browse by: Latest US Patents, China's latest patents, Technical Efficacy Thesaurus, Application Domain, Technology Topic, Popular Technical Reports.
© 2025 PatSnap. All rights reserved.Legal|Privacy policy|Modern Slavery Act Transparency Statement|Sitemap|About US| Contact US: help@patsnap.com