Method and system for processing red mud to recycle refined iron powder
A technology for recovering iron and red mud, applied in the direction of improving process efficiency, can solve the problems of high content of reducing gas CO, long roasting time, and high energy consumption, and achieve high iron recovery rate, reduced roasting energy consumption, and energy consumption. low effect
- Summary
- Abstract
- Description
- Claims
- Application Information
AI Technical Summary
Problems solved by technology
Method used
Image
Examples
Embodiment 2
[0061] The Bayer process red mud of an aluminum factory in Shandong, with a total iron grade of 27.3%, obtained a high-strength magnetic concentrate with a total iron grade of 35.3% after strong magnetic roughing, which reduced the amount of roasting in the furnace by 36%. After flash magnetization roasting-weak magnetic After selection, the beneficiation indicators of 61-62% iron concentrate grade, 53-56% yield, 85-89% iron recovery rate and 9-13% iron grade of tailings were obtained. Calculated based on the current market price of 60% iron ore powder products with a total iron grade of 500 yuan / ton, 2 million tons of red mud can be processed annually, and 650,000 tons of iron ore powder can be obtained, realizing an annual output value of 325 million yuan; The amount of mud discharged saves the capital construction and maintenance costs of the tailings dam.
Embodiment 3
[0063] The red mud of a domestic aluminum factory has a total iron grade of 20.5%. After strong magnetic roughing, a strong magnetic concentrate with a total iron grade of 30% is obtained, which reduces the amount of roasting in the furnace by 60%. After flash magnetization roasting-weak magnetic separation , obtained the beneficiation indexes of 60-61% iron concentrate grade, 48-51% yield, 82-85% iron recovery rate and 10-13% iron grade of tailings. Calculated based on the current market price of 60% iron ore powder products with a total iron grade of 500 yuan / ton, 2 million tons of red mud can be processed annually, and 330,000 tons of iron ore powder can be obtained, realizing an annual output value of 165 million yuan; The amount of mud discharged saves the capital construction and maintenance costs of the tailings dam.
[0064] In addition, after the implementation of the present invention, not only the fine iron powder is recovered, but also other valuable metals in the ...
PUM
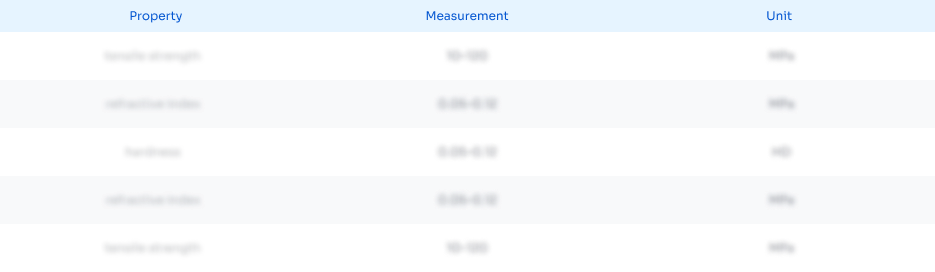
Abstract
Description
Claims
Application Information

- R&D Engineer
- R&D Manager
- IP Professional
- Industry Leading Data Capabilities
- Powerful AI technology
- Patent DNA Extraction
Browse by: Latest US Patents, China's latest patents, Technical Efficacy Thesaurus, Application Domain, Technology Topic, Popular Technical Reports.
© 2024 PatSnap. All rights reserved.Legal|Privacy policy|Modern Slavery Act Transparency Statement|Sitemap|About US| Contact US: help@patsnap.com