Deep deoxidizing apparatus and application thereof
A deep deoxidation and deoxidizer technology, applied in the field of deep deoxidation devices, can solve the problems of expensive platinum catalysts, insufficient deoxidation precision, and low deoxidation capacity, and achieve reduced deoxidation effect, fast deoxidation speed, and large deoxidation capacity. Effect
- Summary
- Abstract
- Description
- Claims
- Application Information
AI Technical Summary
Problems solved by technology
Method used
Image
Examples
Embodiment 1
[0068] The raw material Ar gas flow is set at 250ml / min, the temperature is kept constant at 300°C, and Figure 5 It is a schematic diagram of the change of oxygen content after 2 h of flowing Ar gas. After 184 minutes of the test, the oxygen content at the inlet and outlet of the furnace decreased to 1.79×10 -11 / 2.34×10 -5 ppm; after another 55 minutes, the oxygen content at both ends was basically stable at 10 -11 ppm, with an average of 1.442×10 -11 / 5.470×10 -11 ppm.
Embodiment 2
[0070] Example 2 is following Example 1, and the gas temperature is changed to 400°C, that is, after Ar gas is still introduced at 250ml / min for 132min, the oxygen content at the inlet and outlet is finally reduced to 10 -15 / 10 -14 ppm, see the attached schematic diagram for the change of oxygen content Figure 5 . It can be seen from the figure that the oxygen content decreases steadily, and the average oxygen content at the intake end is 4.55×10 -15 ppm, the average oxygen content at the gas outlet is 4.15×10 -14 around ppm, which will further reduce the oxygen content over time.
Embodiment 3
[0072] Compared with Example 1, the difference is that Ar-10%H was introduced when the gas temperature was 300°C 2 Mixed gas, namely Ar, H 2 The flow rates were adjusted to 250 and 25ml / min respectively. After 200 minutes, the oxygen content at the inlet and outlet was stabilized at 10 -19 / 10 -18 ppm, the schematic diagram of oxygen content change after 144min is attached Figure 6 . It can be seen from the figure that when Ar and H 2 Mixed gas, the oxygen content is greatly reduced, and after 344 minutes of the experiment, the oxygen content at the inlet end changes slightly, and the oxygen content at the outlet end may be affected by the mixed gas flow in the furnace. ppm).
PUM
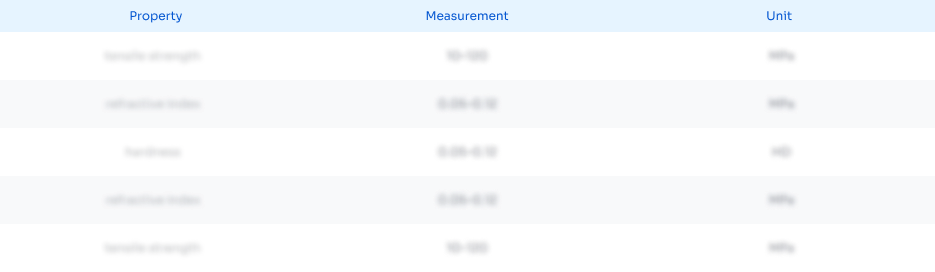
Abstract
Description
Claims
Application Information

- R&D
- Intellectual Property
- Life Sciences
- Materials
- Tech Scout
- Unparalleled Data Quality
- Higher Quality Content
- 60% Fewer Hallucinations
Browse by: Latest US Patents, China's latest patents, Technical Efficacy Thesaurus, Application Domain, Technology Topic, Popular Technical Reports.
© 2025 PatSnap. All rights reserved.Legal|Privacy policy|Modern Slavery Act Transparency Statement|Sitemap|About US| Contact US: help@patsnap.com