Production process for engine flywheel
A production process and engine technology, applied in the field of the production process of the engine flywheel, can solve the problems of high production costs, complex process routes, and large energy consumption, saving labor and energy, good workshop environment, and high material utilization. Effect
- Summary
- Abstract
- Description
- Claims
- Application Information
AI Technical Summary
Problems solved by technology
Method used
Examples
Embodiment 1
[0022] A production process for an engine flywheel, comprising the following steps:
[0023] 1) Production of flexible discs, blank turning processing, and lathing out of the flexible discs. The flexible discs are punched with mounting holes and riveting holes, and the mounting holes and riveting holes are rounded to remove surface burrs;
[0024] 2) Production of ring gears;
[0025] 3) Process the teeth on the outer side of the ring gear by the hobbing machine, the speed of the hobbing machine is 80r / min, and the processing time is 5min;
[0026] 4) Assemble the flexible disk and the ring gear by hot pressing, heat the ring gear at 280°C for 30 minutes, take it out, heat press it onto the flexible disk by the press machine, cool it naturally, and carry out the assembly and pinning process;
[0027] 5) Inspection process. The inspection process includes dynamic balance inspection and routine inspection. The dynamic balance inspection ensures the balance of the entire flywhee...
Embodiment 2
[0031] The different process steps from Example 1 are that the speed of the gear hobbing machine is 0 r / min, and the processing time is 3 minutes; the ring gear is heated at 250° C. for 45 minutes.
Embodiment 3
[0033] The different process steps from Example 1 are that the speed of the gear hobbing machine is 85r / min, and the processing time is 4min; the ring gear is heated at 265°C for 37min.
[0034] Since the flywheel disc is produced by stamping technology, the process is simpler and more reshaped, and the precision of the parts can be fully guaranteed. A lot of labor and energy are saved, and the production cost of the product is greatly reduced. The butt welding process is adopted to produce the ring gear blank, the blank production efficiency is high, and the workshop environment is good. Low material consumption and high material utilization. 45# cold-drawn round steel is selected, with high dimensional accuracy, and the machining allowance is only 1mm to ensure the accuracy of the parts. In addition, because the signal teeth are half-open teeth, the teeth can be punched first and then formed in the process, which can effectively improve the production efficiency and the pr...
PUM
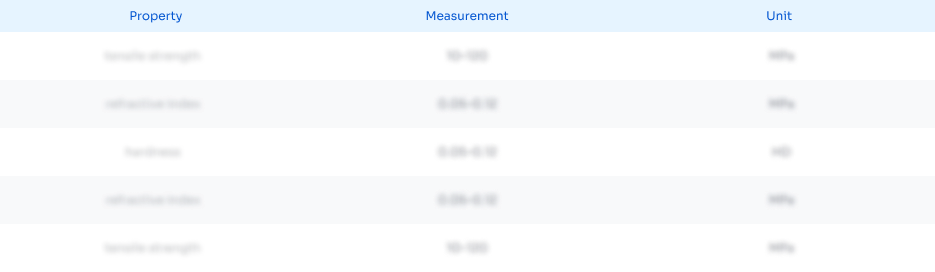
Abstract
Description
Claims
Application Information

- R&D Engineer
- R&D Manager
- IP Professional
- Industry Leading Data Capabilities
- Powerful AI technology
- Patent DNA Extraction
Browse by: Latest US Patents, China's latest patents, Technical Efficacy Thesaurus, Application Domain, Technology Topic, Popular Technical Reports.
© 2024 PatSnap. All rights reserved.Legal|Privacy policy|Modern Slavery Act Transparency Statement|Sitemap|About US| Contact US: help@patsnap.com