Passive magnetic combined vibration damping device for inclinometer while drilling
A technology of inclinometer while drilling and vibration damping device, which is applied in the direction of measurement, earthwork drilling, wellbore/well parts, etc., which can solve the problems of rubber temperature rise, damping and vibration reduction effect, accelerated rubber aging, etc., to achieve Weak damping effect, overcome rubber aging, strong damping effect
- Summary
- Abstract
- Description
- Claims
- Application Information
AI Technical Summary
Problems solved by technology
Method used
Image
Examples
Embodiment Construction
[0015] As shown in Figure 1, a passive magnetic combination damping device for inclinometers while drilling can be used for vibration protection of inclinometers while drilling, wherein: the inclinometer system includes: shunt connector 1, upper probe 2 , battery short section 9, connecting head 10, lower probe tube 11, circuit short section 12, measuring short section 15 and guide shoes 16; the axial damping system includes: first plug 3a, second plug 3b, third plug 3c, the fourth plug 3d, the fifth plug 3e, the first sliding bearing 4a, the second sliding bearing 4b, the third sliding bearing 4c, the fourth sliding bearing 4d, the fifth sliding bearing 4e, the first moving magnetic steel assembly 5a, The second moving magnet steel assembly 5b, the third moving magnet steel assembly 5c, the fourth moving magnet steel assembly 5d, the fifth moving magnet steel assembly 5e, the first cylinder 6a, the second cylinder 6b, the third cylinder 6c, The fourth cylinder 6d, the fifth c...
PUM
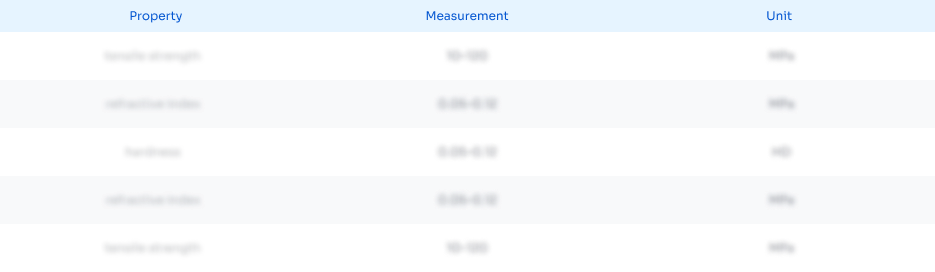
Abstract
Description
Claims
Application Information

- R&D Engineer
- R&D Manager
- IP Professional
- Industry Leading Data Capabilities
- Powerful AI technology
- Patent DNA Extraction
Browse by: Latest US Patents, China's latest patents, Technical Efficacy Thesaurus, Application Domain, Technology Topic, Popular Technical Reports.
© 2024 PatSnap. All rights reserved.Legal|Privacy policy|Modern Slavery Act Transparency Statement|Sitemap|About US| Contact US: help@patsnap.com