Preparation method of natural-melanin-base epoxy resin
A natural melanin-based epoxy resin technology, applied in the field of bio-based resin preparation, can solve problems such as epoxy resins that have not yet been seen, and achieve the effects of improving production and working conditions, eliminating pollution, and high efficiency
- Summary
- Abstract
- Description
- Claims
- Application Information
AI Technical Summary
Problems solved by technology
Method used
Image
Examples
Embodiment 1
[0028] Such as figure 1 As shown, take 10g of black sesame seed coat melanin and put it into a reactor with a volume of 1000mL, add 600mL of N,N-dimethylformamide for washing to fully dissolve the melanin, then add 355g of epichlorohydrin, heat up to 90°C, After reacting for 4 hours, cool to room temperature and centrifuge at 5000g for 5 minutes, wash the obtained precipitate with 300mL N,N'-dimethylformamide, and then centrifuge at 5000g for 5 minutes, repeat this process twice, and collect the precipitate That is, natural melanin epoxy resin is obtained.
Embodiment 2
[0030] Such as figure 1 As shown, take 10g of chestnut shell pigment and put it into a reactor with a volume of 1000mL, add 500mL of N,N-dimethylformamide to wash, fully dissolve the melanin, then add 4g of epichlorohydrin, heat up to 85°C, and react for 8 hours After cooling to room temperature and centrifuging at a centrifugal acceleration of 5000g for 5 minutes, the resulting precipitate was washed with 400mL of ethanol and centrifuged at a centrifugal acceleration of 5000g for 5 minutes, and washed twice in this way. Collect the precipitate to obtain the natural melanin epoxy resin.
Embodiment 3
[0032] Such as figure 1 As shown, take 10g of fungus melanin and put it into a reactor with a volume of 1000mL, add 500mL of N,N-dimethylformamide to fully dissolve the melanin, then add 296g of epichlorohydrin, raise the temperature to 85°C, and react for 16 hours. Cool and filter with filter paper, wash the precipitate with 250mL methanol and filter the filter residue, and repeat the washing twice. Collect the filter residue to obtain natural black pigment epoxy resin.
PUM
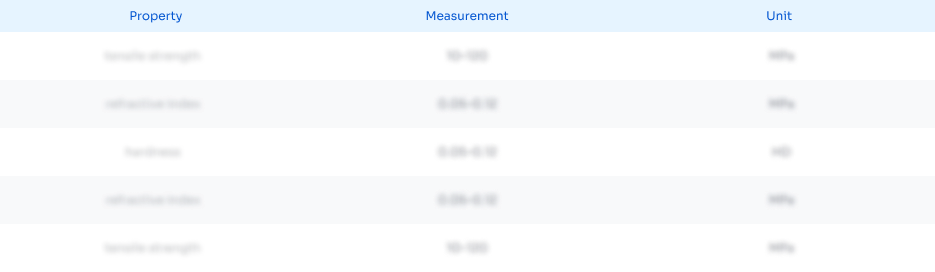
Abstract
Description
Claims
Application Information

- R&D Engineer
- R&D Manager
- IP Professional
- Industry Leading Data Capabilities
- Powerful AI technology
- Patent DNA Extraction
Browse by: Latest US Patents, China's latest patents, Technical Efficacy Thesaurus, Application Domain, Technology Topic, Popular Technical Reports.
© 2024 PatSnap. All rights reserved.Legal|Privacy policy|Modern Slavery Act Transparency Statement|Sitemap|About US| Contact US: help@patsnap.com