Slow and controlled release coating tablet dissolution degree stability improving method
A technology of coated tablets and dissolution rate, which is applied in sugar-coated pills, devices for making drugs into special physical or taking forms, material inspection products, etc. Problems such as inability to control the quality of the production process
- Summary
- Abstract
- Description
- Claims
- Application Information
AI Technical Summary
Problems solved by technology
Method used
Image
Examples
Embodiment 1
[0040] Add 0.625 mg solid sustained-release preparation tablet cores into the coating pan, adjust the gas flow to make the solid tablet core temperature reach 42°C, and then start to gradually spray the pre-prepared 8% Opadry and Coating solution of ethanol solvent. Start timing with a stopwatch, and record the time from the beginning of adding the coating solution to the end of adding the coating solution and the time of adding calcium sulfate powder. A total of 2.26 L of coating solution was added after 32 seconds. After adding the coating solution, the operator observed the dryness of the tablet core, and added the calcium sulfate powder at 192 seconds. When the coating starts, the ethanol measuring device starts to measure the concentration of ethanol in the tail gas in the coating pan, and records the data every 5 seconds until it is completed at 350 seconds. Experimental results such as figure 1 with figure 2 shown. Experiments have shown that the best time to add ...
Embodiment 2
[0042] Add the solid sustained-release preparation tablet core with a specification of 1.25 mg into the coating pan, adjust the gas flow to make the solid tablet core temperature reach 42°C, and then start to gradually spray the pre-prepared tablet core containing 8% Opadry and Coating solution of ethanol solvent. Start timing with a stopwatch, and record the time from the beginning of adding the coating solution to the end of adding the coating solution and the time of adding calcium sulfate powder. A total of 2.46 L of coating solution was added after 37 seconds. After adding the coating solution, the dryness of the tablet core was observed by the operator, and the calcium sulfate powder was added in 200 seconds. At the same time when the coating starts, use the ethanol measuring device to start measuring the concentration of ethanol in the tail gas in the coating pan, and record the data every 5-10 seconds until it is completed at 420 seconds. Experimental results such as...
Embodiment 3
[0044]Add the solid sustained-release preparation tablet core with a tablet weight of 300 mg into the coating pan, adjust the gas flow to make the temperature of the solid tablet core reach 42°C, and then start to gradually spray the pre-prepared 8% Oubadi into the core. Alternative and ethanol solvent coating solution. Start timing with a stopwatch, and record the time from the beginning of adding the coating solution to the end of adding the coating solution and the time of adding calcium sulfate powder. When the empirical operation method is used, there is tablet adhesion during the coating process, and about 10% of the prepared coated tablets have cracks and breakages on the surface. After applying the method of the present invention, there is no adhesion phenomenon in the tablet during the coating process, and the surface of the prepared coated tablet is intact without damage.
PUM
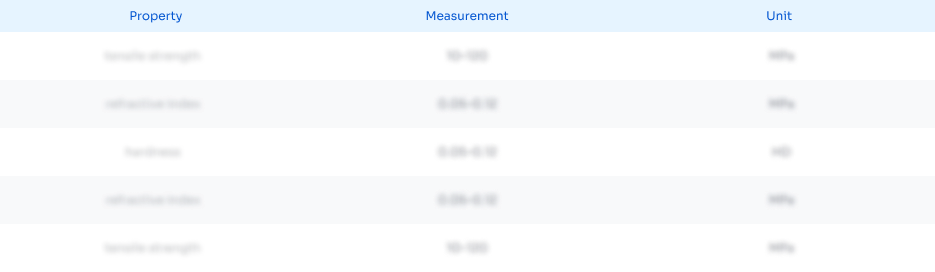
Abstract
Description
Claims
Application Information

- Generate Ideas
- Intellectual Property
- Life Sciences
- Materials
- Tech Scout
- Unparalleled Data Quality
- Higher Quality Content
- 60% Fewer Hallucinations
Browse by: Latest US Patents, China's latest patents, Technical Efficacy Thesaurus, Application Domain, Technology Topic, Popular Technical Reports.
© 2025 PatSnap. All rights reserved.Legal|Privacy policy|Modern Slavery Act Transparency Statement|Sitemap|About US| Contact US: help@patsnap.com