Flexible hinge amplification-based piezoelectric microgripper
A flexible hinge and micro-clamp technology, applied in the field of micro-clamps, can solve the problems that the displacement cannot be directly related, difficult to integrate into the micro-operating system, and the position of the lever fulcrum is not clear. Wide range, small size effect
- Summary
- Abstract
- Description
- Claims
- Application Information
AI Technical Summary
Problems solved by technology
Method used
Image
Examples
Embodiment Construction
[0030] With reference to accompanying drawing, further illustrate the present invention:
[0031] Such as figure 1As shown, the piezoelectric micro-clamp based on flexible hinge amplification includes a base, a frame 31 fixed on the base, a piezoelectric stack driver 2 is installed on the frame 31, and the pretension of the piezoelectric stack driver 2 Screw 1, motion transmission mechanism, a pair of clamping arms 35 and chucks mounted on the head ends of the clamping arms 35, the motion transmission mechanism converts the deformation of the piezoelectric stack driver 2 into the displacement of the clamping head 4; the frame 31 has a For the symmetrically arranged columns 331, the piezoelectric stack driver 2 is located between the two columns 331; the motion transmission mechanism includes a pair of double rocker mechanisms and a pair of lever arms 36 symmetrically arranged on both sides of the piezoelectric stack driver 2 One end of the active rocker 34 of the double rocke...
PUM
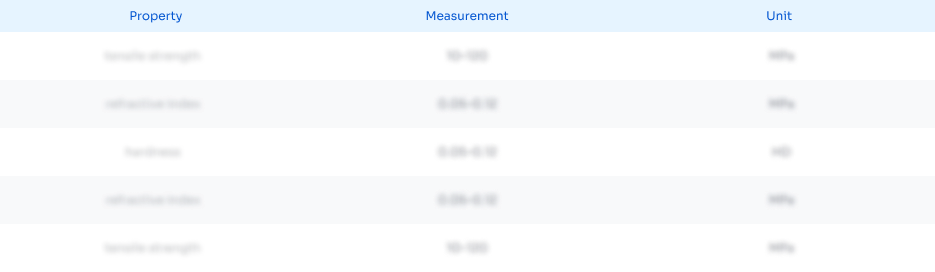
Abstract
Description
Claims
Application Information

- R&D Engineer
- R&D Manager
- IP Professional
- Industry Leading Data Capabilities
- Powerful AI technology
- Patent DNA Extraction
Browse by: Latest US Patents, China's latest patents, Technical Efficacy Thesaurus, Application Domain, Technology Topic, Popular Technical Reports.
© 2024 PatSnap. All rights reserved.Legal|Privacy policy|Modern Slavery Act Transparency Statement|Sitemap|About US| Contact US: help@patsnap.com