A countersunk hole processing method of wear-resistant liner
A processing method and technology of wear-resistant liners, which are applied in the field of hole processing, can solve the problems of inconvenient processing methods for countersink holes of wear-resistant liners, short life of drill bits, and increased processing costs, so as to achieve reasonable design of manufacturing steps and reduce Processing cost, effect of ensuring installation size
- Summary
- Abstract
- Description
- Claims
- Application Information
AI Technical Summary
Problems solved by technology
Method used
Image
Examples
Embodiment 1
[0029] The counterbore processing method of the wear-resistant liner of the present invention comprises the following steps:
[0030] a. Lofting and blanking
[0031] Lofting is carried out during the blanking stage to ensure the expanded size of the parts;
[0032] b. Hole opening and pressing
[0033] Taking the maximum diameter of the countersunk part as 40mm as an example, open a round hole with a diameter of 50mm at the position of the countersunk hole required by the drawing, and then press the wear-resistant plate to make it reach the required arc;
[0034] c. Machining countersunk hole parts, including the following steps:
[0035] (1) Round steel blanking, the round steel blanking with an outer diameter of 48mm is selected as the blank of the countersunk hole;
[0036] (2) Drill the center hole and drill the center hole on the blank;
[0037] (3) Drill the countersink, and then drill the countersink on the blank with the center hole drilled;
[0038] (4) Mill the...
PUM
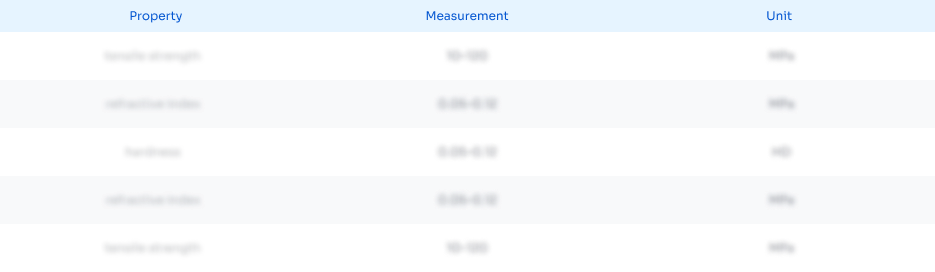
Abstract
Description
Claims
Application Information

- R&D Engineer
- R&D Manager
- IP Professional
- Industry Leading Data Capabilities
- Powerful AI technology
- Patent DNA Extraction
Browse by: Latest US Patents, China's latest patents, Technical Efficacy Thesaurus, Application Domain, Technology Topic, Popular Technical Reports.
© 2024 PatSnap. All rights reserved.Legal|Privacy policy|Modern Slavery Act Transparency Statement|Sitemap|About US| Contact US: help@patsnap.com